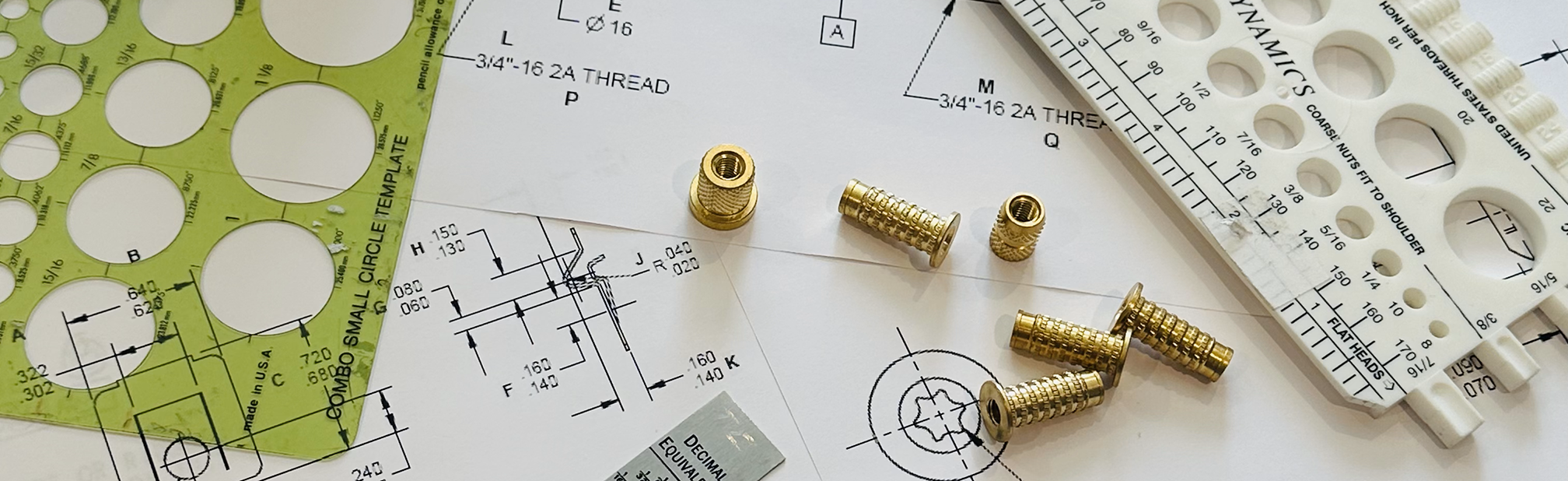
As car designers accelerate the integration of lightweight materials into vehicle designs, collaboration between plastics and fastener engineers has become an imperative. Nowhere is this more evident than during the prototyping and pre-production stages, where fastener choices can significantly influence part performance, manufacturability, and long-term durability.
When fastener integration is treated as an afterthought in plastic component design, the result is often compromised joint performance, unpredictable assembly behavior, and costly tooling rework. But when fastener and plastics engineers collaborate early in the development cycle, they can preempt these issues by aligning mechanical performance with real-world manufacturing constraints.
Design Problems That Start at the Interface
Even at the Tier 1 and OEM levels, many design pitfalls stem from poor interaction between plastic materials and fasteners:
- Cracked bosses and failed threads due to unoptimized boss geometry or unsupported torque specs
- Assembly misalignment when mating components are not co-designed for fastener-driven fit
- Material creep and stress relaxation, especially in thermoplastics under continuous mechanical load
- Excessive cycle times or scrap from fastener insertion problems during prototyping
These problems are often discovered in the prototype stage—too late for low-cost design corrections, and just early enough to cause delays in downstream validation.
Why OEM Engineers Should Prioritize Fastener Collaboration in Early Design
By involving fastener experts early—during initial CAD reviews and DFMEA stages—OEM and Tier 1 design teams can:
- Optimize boss and wall thickness to handle insertion forces and long-term stress
- Select proper thread geometries (e.g., trilobular, double-lead, or HI-LO) based on resin type and assembly torque targets
- Evaluate heat staking vs. press-fit vs. thread-forming inserts with the chosen plastic and projected loading environment
- Pre-qualify joint configurations for vibration, thermal expansion, and pull-out resistance before tool steel is cut
Case for Co-Validation During Prototyping
OEM prototyping labs increasingly include validation of joint strength, torque retention, and thread engagement during early trials. But meaningful results require input from both plastics and fastener disciplines:
- FEA can model stress flow around the joint, but accurate boundary conditions depend on fastener drive torque and clamping behavior.
- Fastener pull-out and strip-out testing must be matched to resin properties and prototype process conditions (e.g., injection molding variance).
- Thermal cycling and creep tests must simulate long-term mechanical loads with fastener-plastic combinations representative of final builds.
The result: faster identification of risk areas, fewer late-stage tooling changes, and more consistent validation results from prototype to PPAP.
Real-World Collaboration: A Competitive Advantage
Leading OEMs are treating fasteners as engineered components—not catalog items—especially when dealing with multi-material joints. By sourcing fasteners and inserts alongside molded parts during early prototyping, they:
- Eliminate misalignment between CAD and actual part performance
- Streamline validation timelines by working with component-level data from both sides
- Reduce part count and improve access in tight packaging spaces through shared design review
Final Thoughts
The interface between fasteners and plastic components is where many unseen performance and production issues originate. For OEMs and Tier 1 suppliers working under tight timelines and cost constraints, cross-functional collaboration between plastics and fastener experts during design and prototyping isn’t just best practice—it’s essential to program success.
Need support integrating fastening strategy into your next prototype or design freeze?
At Components for Industry (CFI), we partner directly with your team to optimize fastener selection and joint design for plastic components—ensuring strong, reliable assemblies before they reach production.