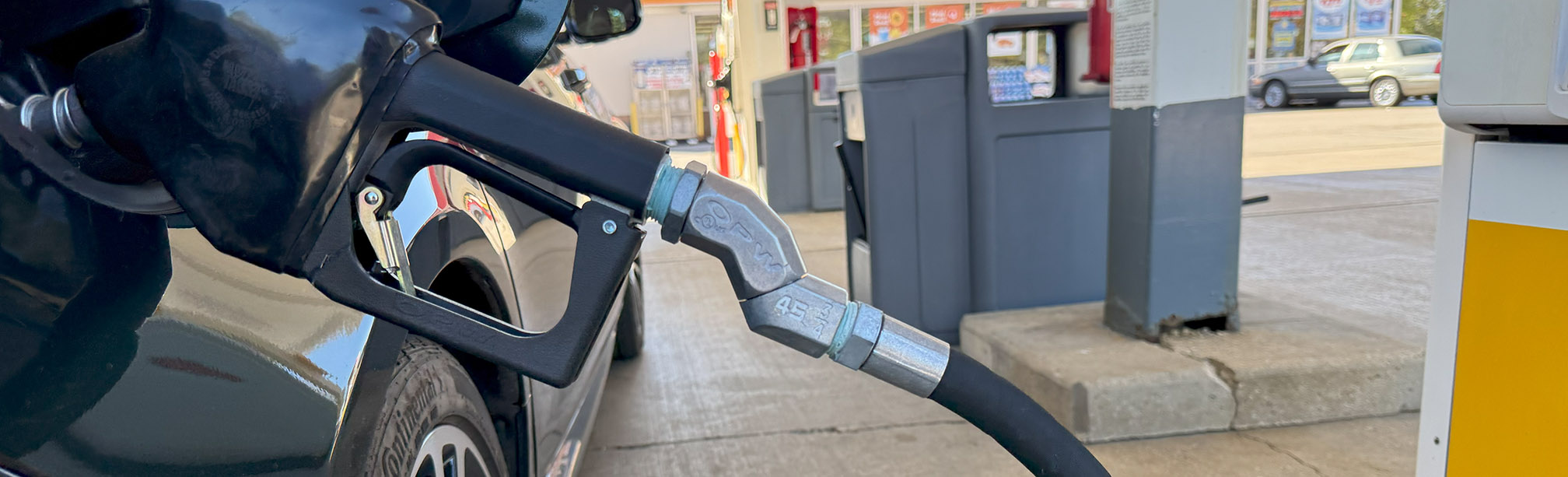
How custom components can help enhance durability in automotive assemblies while helping achieve bigger goals like emission standards for automakers
In 2024, the CAFE standards for passenger cars stand at 54.5 MPG and are set to increase at 2% year over year for model year 2027 through 20311. Those kinds of drastic goals in the automotive industry are simply unachievable without utilizing next-generation composites and lightweight materials in automotive assemblies. However, utilizing those next-generation composites and lightweight materials are also unachievable without utilizing threaded inserts.
Threaded inserts improve durability in automotive assemblies by helping achieve the common challenges of adding strength in fastening with softer, lightweight materials like plastics, composites and aluminum. Those lighter materials – even the strongest ones – have downsides like brittleness compared to heavier steels; thermal expansion mismatch between bonded parts; and simple joining and fastening challenges that all can be corrected through the right fasteners.
What are the current CAFE standards?
Today, Corporate Average Fuel Economy (CAFE) standards for passenger cars and light trucks stands at 40 MPG; by 2026, it’s supposed to stand at 49.42. To say those numbers are ambitious would be the understatement of the century. However, automotive engineers are trying to get there with the use of ingenious next generation materials and the prerequisite inserts that go with them.
What is an automotive assembly?
Automotive assemblies refer to the various systems, subsystems, and components that make up a complete vehicle. These assemblies are grouped based on their function, such as engine, transmission, chassis, suspension, brakes, interior, HVAC, exhaust and emissions control, and electrical.
Automotive assemblies are essentially one level up in taxonomy to parts and components. That, however, makes the component no less important because, without components like the threaded insert, engine assemblies such as engine blocks, cylinder heads, intake and exhaust manifolds, and power adders such as superchargers and turbochargers would never fit together.
What role would a threaded insert play in an automotive assembly?
Threaded inserts can play many roles depending upon the application. Inserts are used everywhere from a car’s interior to the engine bay to the exhaust system.
In assemblies like aluminum cylinder heads, brass or stainless steel threaded inserts are often used to create strong ports for spark plugs due to their superior temperature and wear resistance compared to the aluminum head. Without the insert, spark plug port threads could easily strip removing the required ability for repeated removal and installation of spark plugs – rendering the assembly unusable.
To keep up with today’s emission standards, automotive manufacturers have turned away from larger displacement, normally aspirated engines and moved toward smaller displacement forced induction motors that still meet the power demands of today’s customer that still meets gas mileage standards3. This migration has made assemblies like superchargers and turbochargers essential in modern day automobiles.
In superchargers, threaded inserts are utilized everywhere, from the housing to engine block and intake manifold mounting points to their pulley and drive belt systems. These inserts play the critical role of reinforcing mounting points for both the supercharger itself and/or intercooler systems and can withstand the temperature and vibrational stresses created by the impellers, rotors, pulleys and other moving parts in the supercharger.
Outside of the engine bay, threaded inserts also play a role in the interior. They are often used as mating points between metal frames and plastic and composite trim materials such as dashboards, center consoles, steering columns and other interior assemblies. Threaded inserts play the important role of reinforcing attachment points of seatbelt anchors – especially when paired with lighter, aluminum frames, they also prevent plastics from cracking or wearing out around fasteners during installation.
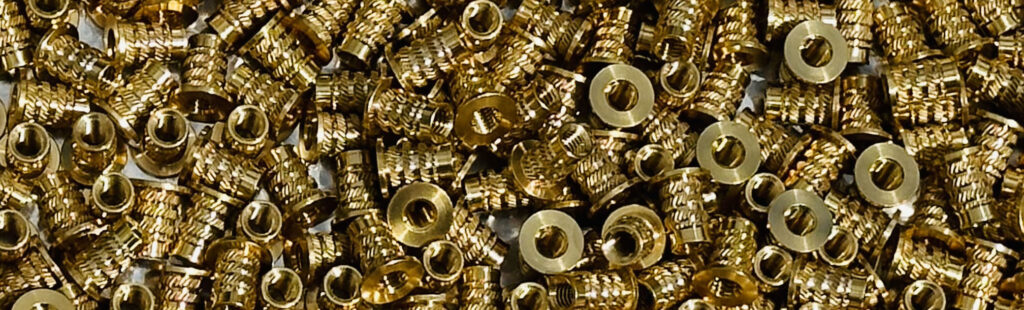
How can threaded inserts help with assembly installation?
As we move further into the 2020s, the CAFE standards are only going to get tighter for automakers, and, in response, the ratio of lighter materials is only going to get higher. Threaded inserts are essential in this world as hard fasteners deform, gall, or tear through, weakening the joint or causing cracks around the fastener – especially when dissimilar materials such as weaker metals, composites and stronger components are paired.
Whether this joint is in a cosmetic interior panel, or an essential engine assembly, automotive assemblies everywhere are subject to significant heat, vibration, and even corrosion concerns if they are not paired with a threaded insert. How can an insert help during initial installation?
By strengthening the threads of an aluminum or composite interface, an insert can protect an automotive assembly from thread stripping during the installation process. In addition, these threads will have increased load-bearing capacity because threaded inserts distribute the load over a larger surface area, improving the overall strength of the assembly. This distributed load minimizes the risk of cracking and material fatigue, preventing stress concentrations.
Most importantly, threaded inserts allow for weight reduction without sacrificing durability. Threaded inserts allow for the use of lightweight materials like aluminum and composites by reinforcing fastener points.
Modern automakers are fighting the fuel mileage battle on two engineering fronts: making their ICE designs more fuel efficient and making the cars themselves lighter through the use of next generation materials. Both fronts require the use of threaded inserts to strengthen interfaces, prevent stripping and increase load capacity – even with the most ingenious next generation materials.
How can CFI help with your company’s Automotive Components?
For over 30 years, Components for Industry has been a worldwide provider in automotive components and a wide number of other industries like Aerospace, Appliance and Heavy Industrial. If you want more information about CFI, our industrial components, our threaded inserts, or our custom design process, contact us at 847-918-0333 or sales@componentsforindustry.com.
- National Highway Traffic Safety Administration (NHTSA). Corporate Average Fuel Economy Standards for Passenger Cars and Light Trucks for Model Years 2027 and Beyond and Fuel Efficiency Standards for Heavy-Duty Pickup Trucks and Vans for Model Years 2030 and Beyond. Obtained from: https://www.nhtsa.gov/sites/nhtsa.gov/files/2024-06/CAFE-2027-2031-HDPUV-2030-2035_Final-Rule_web_0.pdf ↩︎
- Department of Transportation (DOT) National Highway Traffic Safety Administration (NHTSA). Corporate Average Fuel Economy Standars for Model Years 2024-2026 Passenger Cars and Light Trucks. Pg 25735. Obtained from: https://www.govinfo.gov/content/pkg/FR-2022-05-02/pdf/2022-07200.pdf ↩︎
- Car and Driver. Booster Club: How Forced Induction is Changing the Performance Landscape. Obtained from: https://www.caranddriver.com/features/a15120753/booster-club-how-forced-induction-is-changing-the-performance-landscape-feature/ ↩︎