
Why traditional fastener designs may not work
Over the last two decades – especially with the advent of heavy batteries in the automotive industry – the race for lightweight and high-performance composite assemblies has taken center stage. These assemblies, typically made from composites like carbon fiber and CFRP have become especially attractive not only in automotive but other industries including aerospace, consumer electronics and even sports equipment. With this shift in material science comes a shift in the fasteners built to support them.
What has driven this race to the bottom of the scales? Why, in turn, did this cause new fasteners to rise to the forefront?
To understand why both the materials and the fasteners have changed so drastically, let’s take a deep dive into the shear and tensile forces these materials are built to withstand.
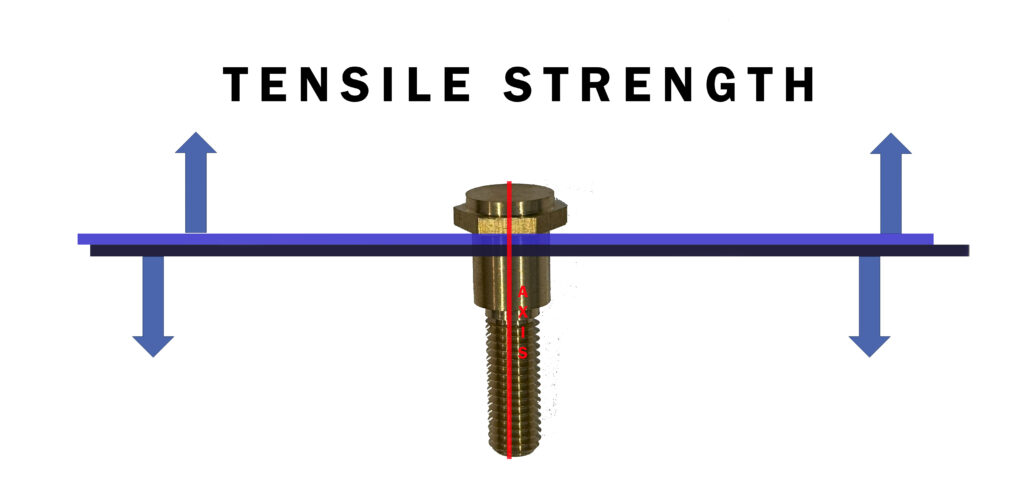
Physics 101: Shear vs. Tensile Forces
- Tensile Force acts along the axis of a fastener, pulling it apart. Imagine two structural panels joined at the ends being pulled directly away from one another along the x-axis. This places axial stress on the fastener. A fastener’s tensile strength is its ability to withstand this force.
- Shear Force acts perpendicular to the fastener, trying to slide the fastener (and joined materials) in opposite directions—like cutting with scissors. Here, the fastener is subjected to transverse forces that can lead to shearing. A fastener’s shear strength is its ability to withstand this force.
Metal fasteners, which are both isotropic and ductile (able to stretch or bend before breaking), are designed to handle both of these forces. However, composites paint a slightly different picture.
Why Traditional Fasteners Have Difficulty with Composites
Composites are anisotropic—meaning their strength and stiffness vary depending on direction. This can presents a big challenge:
🔨 1. Threaded Fasteners Without Inserts Can Crush Composite Layers
Traditional screws and bolts installed directly into carbon fiber reinforced plastics (CFRPs) and composites exert high compressive loads under the head or in the thread region. While CFRPs provide impressive tensile strength, these materials do not handle localized compressive stresses well—leading to delamination or fiber crushing. Without something to distribute the load, the fastener’s head can act like a hole punch, exceeding the compressive limit of the top laminate layer.
🪓 2. Shear Loading Weakens Bonded Areas
Shear forces can cause matrix cracking (small cracks in the binding resin matrix) or fiber pull-out in the laminate layers. This weakens the load transfer and leads to early joint failure, especially if the fastener isn’t designed to distribute load over a wider area.
🧵 3. Tension Can Delaminate the Material
When a fastener pulls upward (tensile load), it can pry apart the composite layers—a condition known as delamination. Without a properly designed insert or support structure, this can happen even under moderate loads.
🔧 Recommended Alternatives (Expanded)
When fastening into composites, it’s important to remember that these materials are stronger in some directions than in others. As a result, concentrated loads in specific areas (like a bolt or screw) can easily crack or damage composites. The following alternatives have been engineered specifically to handle shear and tensile forces more effectively in these advanced materials:
🟡 1. Threaded Inserts
Why they’re superior:
Threaded inserts, especially brass or steel variants, are embedded into the composite during molding or installed using heat or ultrasonic energy. They anchor themselves mechanically or thermally into the substrate, distributing force over a larger area than a direct screw thread.
Scientific advantage:
- Inserts expand the bearing area, lowering compressive stress on the laminate.
- The interference fit (heat or ultrasonic staking) increases pull-out and torque resistance by forming a bond with the resin matrix.
- The insert’s knurling or undercuts mechanically lock the insert in place, reducing the risk of spin-out or stripping under tensile or torsional loading.
Use case: Ideal for assemblies requiring frequent disassembly or torque-tightened joints in thermoplastics or thermoset composites.
🔹 2. Floating Nut Plates
Why they’re superior:
Floating nut plates are fastener assemblies where the nut is free to pivot within a retaining cage. This allows for alignment flexibility during installation and reduces localized stress on the substrate.
Scientific advantage:
- Prevents misalignment-induced stress in brittle composite materials.
- The floating design distributes tensile and shear forces across a wider patch of the composite, especially when combined with large flange heads or countersunk washers.
- Helps avoid the creation of stress risers, which can initiate microcracking and delamination.
Use case: Widely used in aerospace structures where precision assembly and high vibration loads are present.
🔽️ 3. Large-Flange or Countersunk Washers with Compliant Fasteners
Why they’re superior:
Traditional bolts can still be used if paired with engineered components that help manage load paths—such as large-flange washers or compliant fastener systems.
Scientific advantage:
- Flanged surfaces increase bearing area, minimizing compressive damage.
- Some compliant fasteners are designed to absorb vibration and reduce relative motion at the joint, limiting wear and fretting of composite interfaces.
- Washers with tapered countersinks help seat the fastener flush without overloading the fibers at the surface.
Use case: Suitable for moderate-load joints in fiber-reinforced plastics where simplicity and serviceability are priorities.
Conclusion: Think Beyond the Bolt Alone
Composites are revolutionizing engineering, but they demand rethinking fastener design. Ignoring shear and tensile dynamics in composite joints can result in poor performance or even catastrophic failure of the assembly.
Whether you’re building next-gen EV battery enclosures or aerospace panels, choosing the right fastening method isn’t just a detail—it’s mission-critical.
If you’re designing with composites and aren’t sure whether your fasteners are up to the task, contact our engineering team at Components for Industry. We’re happy to help you identify solutions that will stand up to both the load—and the material.