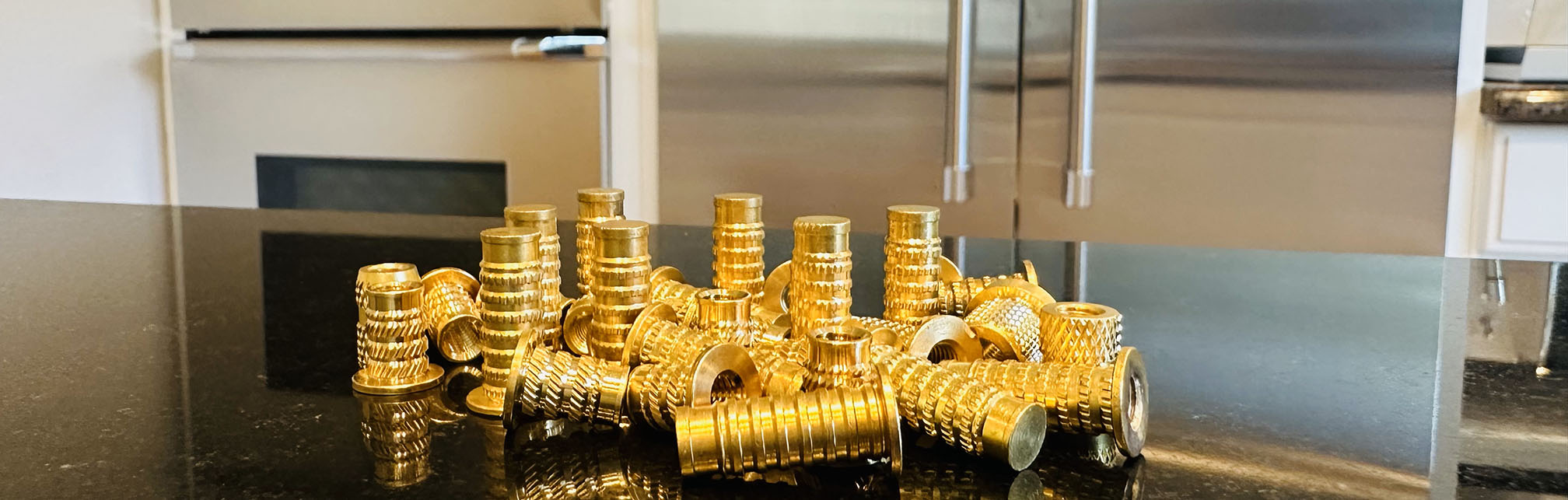
See how the use of exotic materials, plastics and high-stress parts made threaded inserts a vital partner in the Appliance Industry
As we move further into the 2020s, every household appliance seems to get more and more complicated. However, one thing remains the same: the need for seemingly simple, yet oh so important components like threaded inserts. Today, we’ll be answering questions like how these fasteners are used by appliance manufacturers and what specific inserts are utilized in everyday household appliances found in your kitchen and laundry room.
What are threaded inserts?
You are probably familiar with threaded inserts, but for those that aren’t, they are fasteners that provide secure and reusable threaded holes for screws and bolts. These inserts are typically used to strengthen the connection when the base material is not strong enough to ensure long-lasting durability. For example, when screws are over-tightened in plastics or wood, the material can break – threaded inserts can prevent this. Common materials for threaded inserts themselves include brass, stainless steel, and aluminum. Such materials are chosen by corrosion resistance, heat resistance, vibration resistance, and other factors.
Why use Threaded Inserts in Appliance Manufacturing?
Many small home appliances such as coffee makers, blenders and vacuum cleaners are made from lightweight plastics. In addition, many large appliances such as refrigerators, dishwashers and washing machines require threaded inserts to secure plastic parts and housings.
In many appliances, plastics and other composites carry out the vital function of separating water and other liquids from motors and other vital moving parts. Without threaded inserts, composite structures can be weakened and stripped by using fasteners alone. In addition, fasteners can lose their ability to remain tightly secured in the face of mechanical vibration, heat and other long-term wear and tear.
Where are threaded inserts deployed in household appliances?
You will find threaded inserts utilized in a number of places in appliances – especially where there is expected wear and tear from consistent use, heat and vibration. Inserts are used in the attachment points of appliance doors, such as ones found on refrigerators, ovens, dishwashers, and microwaves, due to their constant use and stress. The inserts allow for repeated opening and closing of the doors without the risk of the threads wearing out or stripping and make the doors more reliable and less prone to wear and tear.
Inserts are also utilized in door handles and control panels with buttons, dials or displays. These parts on appliances such as ovens, stoves and other appliances require threaded inserts to beef up fastening points because they are high-touch and are therefore prone to loosening over time. Threaded inserts can not only strengthen the connection between plastic-to-metal connections in the case of control panels, but metal-to-metal connections in the case of stove and oven handles.
What are some of the benefits of utilizing inserts in appliance manufacturing?
Using brass inserts and threaded inserts in general can directly improve the efficiency and cost-effectiveness of appliance manufacturing at scale. Just like in the automotive industry, the use of inserts can directly improve the durability, ease of assembly, cost savings, and design flexibility in the Household Appliance industry.
Threaded inserts offer greater durability than simply using screws and bolts with a lightweight plastic or relatively weaker metal alone. In addition, they simplify the assembly process by creating consistent threads, reducing the time and effort required to fasten components, leading to faster production cycles and greatly reduced labor costs.
This cost savings stretches beyond reduced labor costs and into damage prevention. By standardizing threads, threaded inserts makes it easier to assemble and disassemble appliances during the QC process without damage. This allows manufacturers to avoid costly repairs and replacements during production – this is especially a concern in the appliances industry.
Finally, the use of threaded inserts opens appliance product designers up to a wider range of materials. This started in the automotive industry with the adoption of exotic materials such as carbon fibers to lower weight and boost performance and aesthetics. Use of other exotic composites has spread to the appliance industry1 for weight, renewability/eco-friendliness, and, of course, aesthetics. Use of these composites typically require threaded inserts to properly stand up to the rigors of daily use in a household appliance. So now, designers are free to utilize the latest and greatest composites and meet their wildest designing fantasies.
Conclusion
Threaded inserts will always be an integral part of appliance blueprints, whether you’re talking about large dishwashers and dryers or handheld kitchen gadgets. They ensure reliable, durable connections in soft materials like plastic, streamline assembly processes, and provide flexibility needed for modern appliance designs.
Where does CFI fit in?
For over 30 years, Components for Industry has been a worldwide provider in industrial components such as brass inserts for a wide number of industries like Automotive, Aerospace, Appliance and Heavy Industrial. If you want more information about CFI, our industrial components or our custom design process, contact us at 847-918-0333 or sales@componentsforindustry.com.
Citations
- Market Research Intellect. “Global Plastic Resin for Electrical Appliances Market Size, Scope and Forecast Report.” Obtained hrom: https://www.marketresearchintellect.com/product/global-plastic-resin-for-electrical-appliances-market/ ↩︎