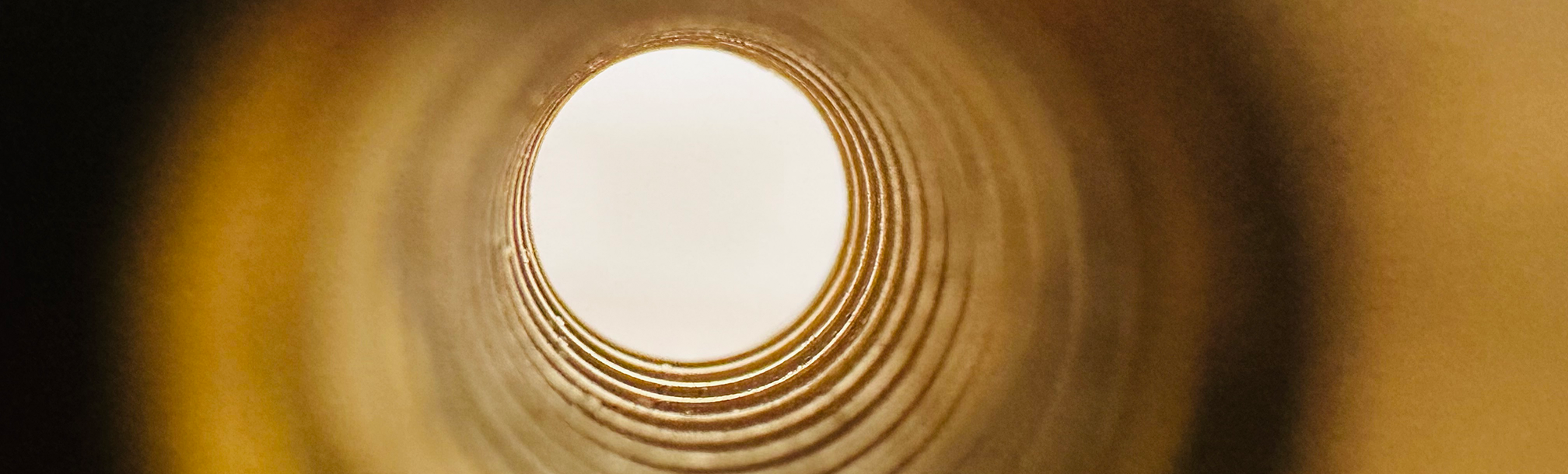
In our previous blog, we covered the basics of threaded inserts and more specifically, brass inserts. However, we only touched upon their use in injection molding applications. As we said in our previous blog, injection molding goes hand-in-hand with brass inserts because inserts offer a strengthened connection between plastics and injection molded parts.
More specifically, inserts offer the following positives over the use of self-tapping screws alone: reusable threads that preserve the bolted joint integrity; more pull-out torque and increased seating torque, and they are not prone to self-tapping screw creep. In addition, inserts provide the strength required to overtighten bolts and screws to stretch fasteners without stripping the threads.
What are the Types of Threaded Inserts for Plastics?
There are four types of threaded inserts for plastics. Each of these types of inserts can be molded in, self-tapped, ultrasonic, pressed in, or installed via heat.
The types of threaded inserts are:
- Expansion Inserts
- Flanged-Type Threaded Inserts
- Male Stud Inserts
- Split Threaded Inserts
What are key characteristics for threaded inserts used with plastics?
Inserts used with injection molded products typically follow some basic design features to ensure that the insert remains mated with the plastic. These features include:
- Knurling Features for Torque Resistance
- Undercuts and Grooves
- Opposing Knurls, Diamond Knurling, and Serrations
- Split Edges cut through pilot hole
- Proportional Length to Desired Pull-Out Resistance
All of these features are unified in the shared goal of increasing pull-out resistance and friction with the mating plastic.
What types of plastics can you use with threaded inserts?
There are two main plastic categories that are used with threaded inserts: thermoplastics and thermosets. Common thermoplastics include ABS, PVC, and polycarbonate. Press-in, Self-Tapping, Heat/Ultrasonic and Molded-In inserts are all used with thermoplastics. Common thermosets include epoxies, polyester resins and Bakelite. Molded-In, Press-In and Self-Tapping Inserts are all used with thermoset plastics.
What kinds of inserts can you use with injection molding applications?
Insert molding actually takes place before the molding process begins. The plastic is then molded around the threaded insert by placing the insert onto a retaining pin holder, sealing the mold tool, and injecting the molten plastic around the threaded insert, permanently mating insert with the plastic.
Many operations automate this process to boost output and cut down on part failure due to cavitation and other factors. Because the threaded insert and all of its knurls, fins and undercut features are molded into the plastic, it has the best performance and lowest failure rate of all the insert types.
In addition to insert molding applications, self-threaded inserts may also be used as they are specifically designed to be used much like a self-tapping screw – they are driven into the plastic until a preset height or torque is achieved and the split edges of the insert cut through the pilot hole to achieve pull-out resistance. Self-threaded inserts are typically used in Automotive applications and are designed for hard and brittle plastics that typically find their way into cars, trucks and SUVs. In addition, self-tapping inserts are quick and easy to install, making them even more attractive to automakers.
What Industries require inserts in plastics?
Product designers utilize inserts in plastics for a wide range of applications including for a number of products that you might find in your home. Aerospace engineers utilize brass inserts in soft and brittle plastics; Automotive engineers use inserts in air intakes; Electronics engineers utilize them in TV housings; Industrial engineers utilize them in power tool housings.
Where does CFI fit in?
For over 30 years, Components for Industry has been a worldwide provider in industrial components such as brass inserts for a wide number of industries like Automotive, Aerospace, Appliance and Heavy Industrial. If you want more information about CFI, our industrial components, our brass inserts, or our custom design process, contact us at 847-918-0333 or sales@componentsforindustry.com.