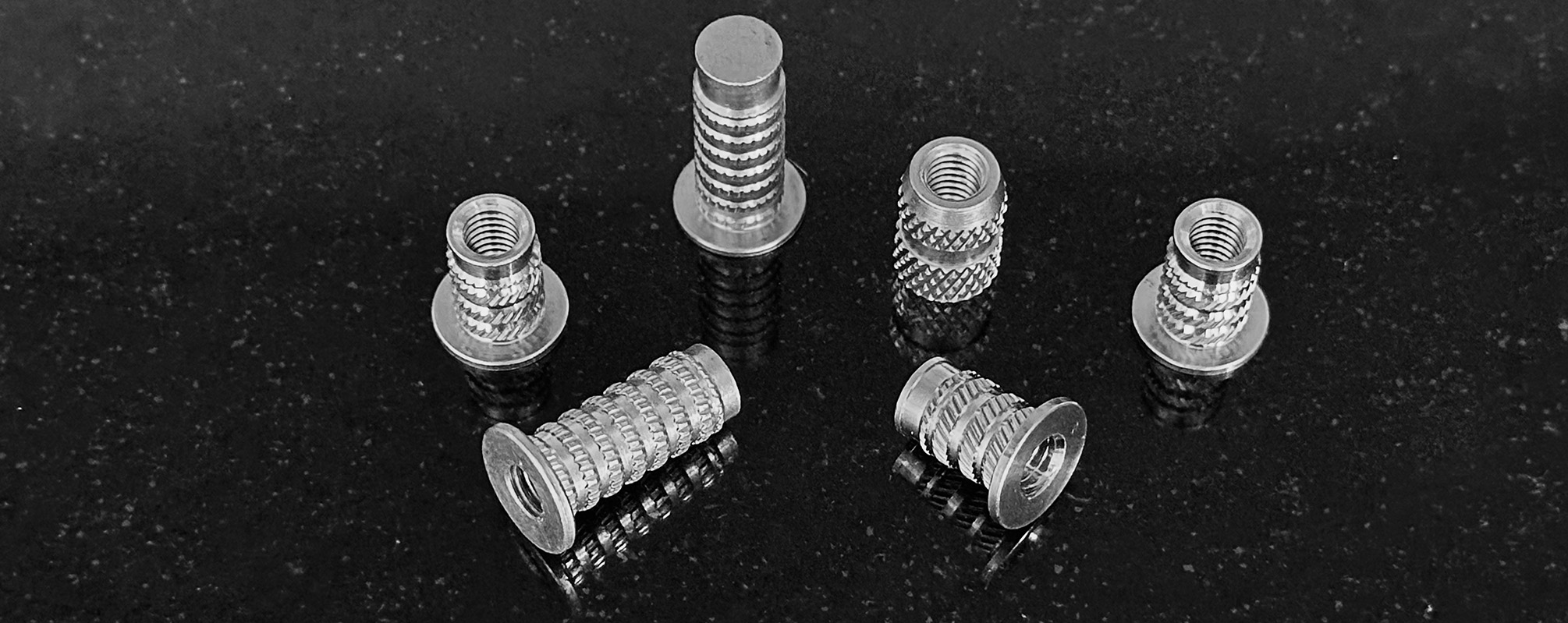
Here at CFI, we’ve been working with components of all kinds for over three decades, including threaded inserts. Typically, inserts are made from brass, due to the material’s versatility thanks to its position in the material science Goldilocks zone of relative strength, cost, corrosion resistance, machinability, thermal conductivity, and lack of magnetic properties. All that said, are threaded inserts made from other materials? Of course they are.
What materials are threaded inserts made from?
In addition to brass, threaded inserts are made from several types of metal and even plastic, depending on their intended application. The following are some of the most common materials outside of brass:
Stainless Steel Inserts
Just like brass, Stainless Threaded Inserts offers excellent corrosion resistance, but it offers higher tensile strength than brass – on the level of 2x the strength of a comparable brass insert. This higher strength makes stainless steel threaded inserts ideal for marine and industrial applications where prolonged exposure to moisture, pressure and chemicals may be a concern. That said, stainless is harder to work with than brass and requires additional machining time. This additional machining time can make stainless steel inserts more expensive than comparable brass inserts.
Carbon Steel Inserts
Steel coated with various materials like zinc, nickel or chromium to enhance corrosion resistance, Carbon Steel Threaded Inserts offer a higher strength alternative to traditional brass inserts thanks to their ability to withstand higher loads and resist wear. In addition to carbon steel’s strength, carbon steel is also a cost-effective alternative compared to other high-strength materials like stainless steel.
Carbon steel must be given a specific corrosion resistance coating chosen for its environmental application as opposed to brass, which offers better corrosion resistance without any coating. In addition, like stainless, carbon steel, while strong, is harder to machine. With the correct coating, carbon steel inserts are used in the automotive industry, heavy machinery, railway and agricultural, and are even used in the marine industry.
Aluminum
Lightweight and resistant to corrosion like brass, though, in its raw form, not as strong as steel or even brass alternatives, aluminum is excellent in applications where weight is a concern. In fact, aluminum (2.7 g/cm3) is on the level of 3x lighter than comparable brass (8.4 g/cm3) inserts. This lack of weight make it an excellent option for automotive and aerospace applications where weight is at a premium and every ounce counts.
Aluminum applications can be strengthened through heat treatment to create aluminum tempers. Aluminum tempers like Aluminum H14, T3 and T6 have tensile strengths that can meet or even exceed brass and mild steel alloys. These tempers, paired with aluminum’s lack of weight make for attractive alternatives for brass and steel threaded inserts.
In addition to weight and corrosion resistance, aluminum threaded inserts offer excellent thermal and electrical conductivity and are non-magnetic like brass inserts. They are also relatively cost effective for lightweight applications and are easy to machine given the lack of tensile strength.
Plastic
Like aluminum, plastic threaded inserts are deployed when weight is the utmost concern. In addition, plastic is significantly lighter than brass, steel and aluminum. Plus, it is inherently corrosion and chemical resistant and provides excellent insulation against electricity. Finally, it is cost-effective, easy to install and easy to machine.
All that said, it has a much lower tensile strength compared to brass, steel and aluminum, and, as a result, is less suitable for high-stress, high-load and high-wear applications. In addition, because plastic is prone to deforming under high temperatures, its use must be limited to applications with limited thermal exposure. Due to its electrical resistance, corrosion resistance and light weight, the consumer electronics, aerospace, robotics and automation, HVAC and automotive industries deploy plastic threaded inserts in specific circumstances where temperature can be controlled.
Where does CFI fit in?
For over 30 years, Components for Industry has been a worldwide provider in industrial components such as brass inserts for a wide number of industries like Automotive, Aerospace, Appliance and Heavy Industrial. If you want more information about CFI, our industrial components, our brass inserts, or our custom design process, contact us at 847-918-0333 or sales@componentsforindustry.com.