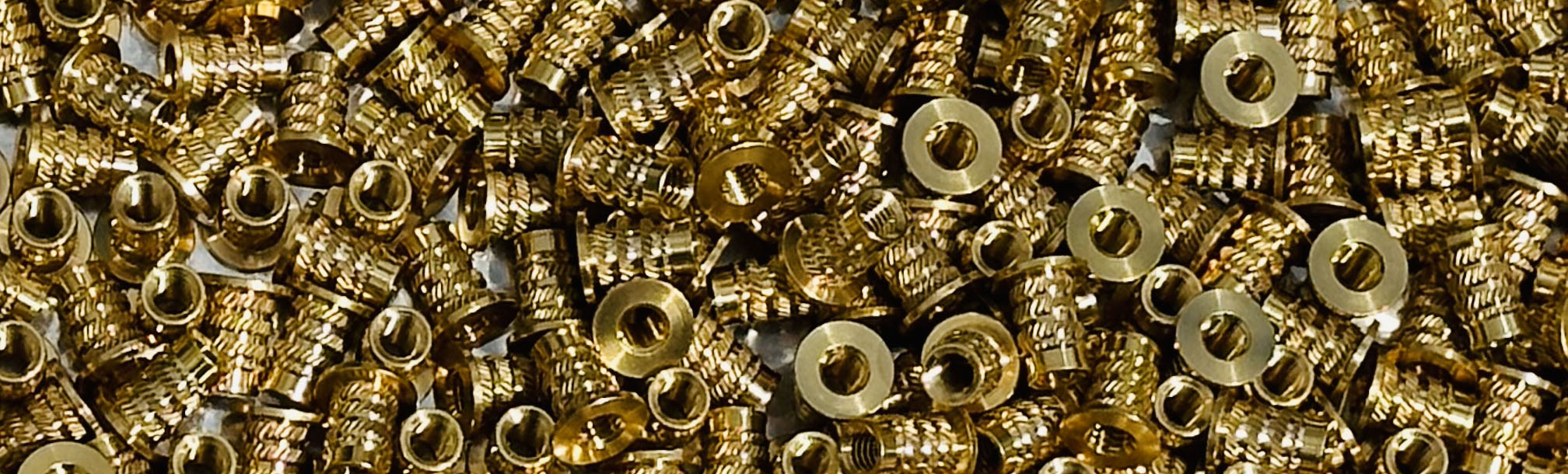
As a direct supplier to automotive OEMs, CFI and its engineers have a lot of experience with automotive components. While many components have a variety of uses, threaded inserts, in particular, are widely utilized throughout the average car. In this blog, we’ll cover the most common types of inserts and how they’re used in automobiles.
Knurled Inserts
Typically heat set when installed into plastic components such as a car’s dashboard, doors, interior panels, and electrical housings, Knurled Inserts can have a number of patterns rolled onto the outside of the workpiece. Depending on the knurl patterns, these inserts exhibit different pull-out and torque resistances.
For example, straight knurls (parallel to the length of the insert) typically offers the greatest resistance to torque, but offers less pull-out resistance. As a result, component engineers might add grooves between knurl bands to increase pullout resistance, depending on the needs of the manufacturer.
Threaded Stud Inserts
Threaded stud inserts are utilized wherever a reusable, durable and most importantly, strong threaded connection is needed in an automobile. These inserts find their way into cars, trucks and SUVs in punishing, (and fail-safe) environments.
Externally Threaded Inserts / Helical Inserts
Typically made from brass for its strength, heat resistance and corrosion resistance, helical inserts are used in engine blocks to reinforce threads to prevent stripping and ensure a stronger long-term connection. Used in restorations of damaged spark plug ports, carburetor fuel inlets, transmission housings, oil drain plugs, exhaust and intake manifolds, head bolt holes, brake calipers, and more in the automotive aftermarket.
Ultrasonic Inserts
Ultrasonic inserts are made for post-mold installation in thermoplastics by quite literally pressing the inserts into the plastics via high-frequency vibration. These frequencies warm up and melt the surrounding plastics, allowing for easy insertion. When the vibration stops, the temperature lowers, the plastic solidifies, and the inserts are permanently locked into place.
These types of inserts are used in composite or plastic components with complex shapes and thin walls such as electric housings, airbag modules, sensor mounts, ECUs, etc. Ultrasonic inserts maintain their integrity and won’t deform in high-temperature environments, so they can also be used where the threaded inserts will be exposed to high temperatures such as engine bays and exhaust systems. This ability to maintain integrity and not crack under heavy load also makes ultrasonic inserts a good candidate for safety equipment, brackets, clips, mounts, and other areas that require a strong, reliable threaded connection.
We hope you enjoyed our synopsis of some of the types of automotive threaded inserts.
Where does CFI fit in?
For over 30 years, Components for Industry has been a worldwide provider in industrial components such as brass inserts for a wide number of industries like Automotive, Aerospace, Appliance and Heavy Industrial. If you want more information about CFI, our industrial components or our custom design process, contact us at 847-918-0333 or sales@componentsforindustry.com