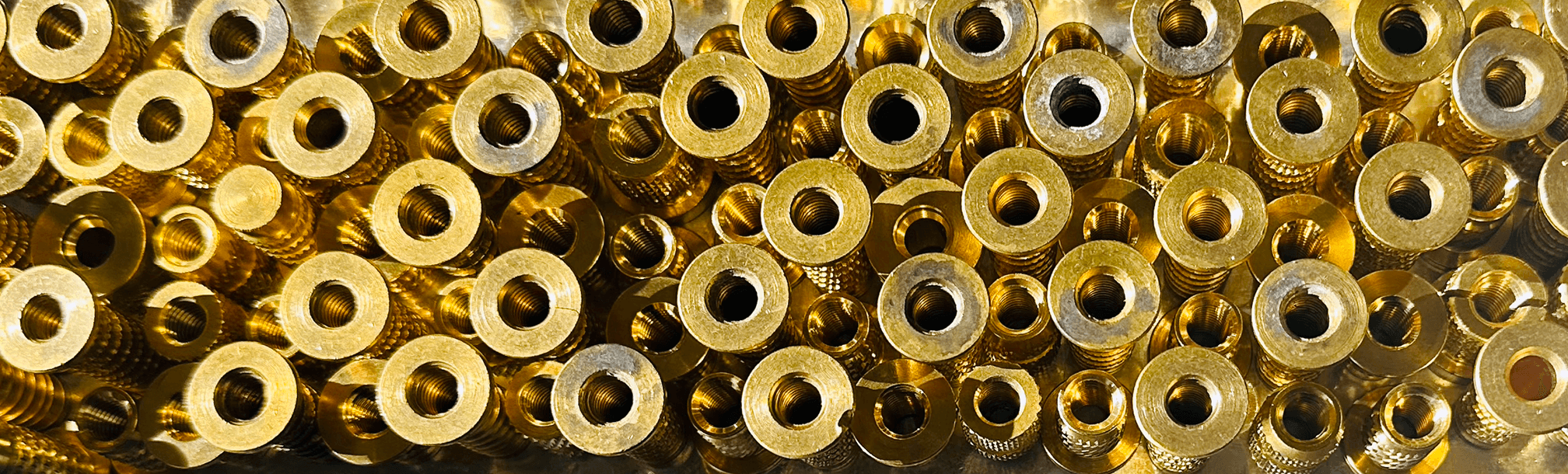
Threaded inserts are utilized to strengthen and add threads to all kinds of materials, from plastics, to composites, to woods. But, how are they utilized in the automotive sector? Inserts have found their way into cars, trucks and SUVs for a wide range of uses, from interior components, to the body and chassis to the engine bay. Basically, if you’ve got a modern car, and you’ve got a major part, a threaded insert won’t be far away.
Essentially, if an automotive OEM needs a threaded hole to be added post production, an insert is going into the car, truck or SUV.
What are inserts used for in cars, trucks and SUVs?
Before we make generalizations, let’s break down a car into basic areas such as the Engine and Transmission; Interior; Suspension and Steering Components; and Underbody and Exhaust.
Engine and Transmission – Threaded inserts are typically used as engine and transmission mounts to hold the drivetrain in place. With proprietary designs, they can provide custom-built solutions that can withstand the vibration from traditional ICE powertrains. In electrical and ICE automobiles alike, inserts are used for heat shield mounts protecting sensitive components (and passengers) from excessive heat.
Interior – Threaded inserts are typically found in seat mountings, seat belts, steering wheel, steering wheel hub and airbag assemblies. They are used wherever there needs to be a component hard-mounted to the car. Threaded inserts are also used to secure panels, brackets and other components to dashboard assembly itself.
Suspension and Steering Components – Just as with drivetrain brackets, inserts are used as suspension and steering brackets to attach suspension components such as control arms, shock absorbers and sway bars to the chassis.
Underbody and Exhaust – Threaded inserts also attach exhaust system components. They are used to attach oxygen sensor connectors and as attachment points for exhaust system clamps and support brackets.
What materials of inserts are used in automotive?
The inserts utilized in automotive applications vary by their purpose. As with any industry, the inserts are engineered for their specific application. Steel and stainless steel are used where strength and durability are championed, such as engine, suspension components and exhaust components. Stainless steel is used when corrosion resistance is needed, such as exhaust systems that are exposed to the elements.
Brass and aluminum are also lightweight, which is important in designing car components. Both also have excellent natural corrosion resistance whereas steel requires a protective coating.
How can CFI help automotive suppliers and manufacturers?
For over 30 years, Components for Industry has been a worldwide provider in industrial components such as brass, steel and aluminum inserts for a wide number of industries like Automotive, Aerospace, Appliance and Heavy Industrial. If you want more information about CFI, our industrial components, our threaded inserts, or our custom design process, contact us at 847-918-0333 or sales@componentsforindustry.com.