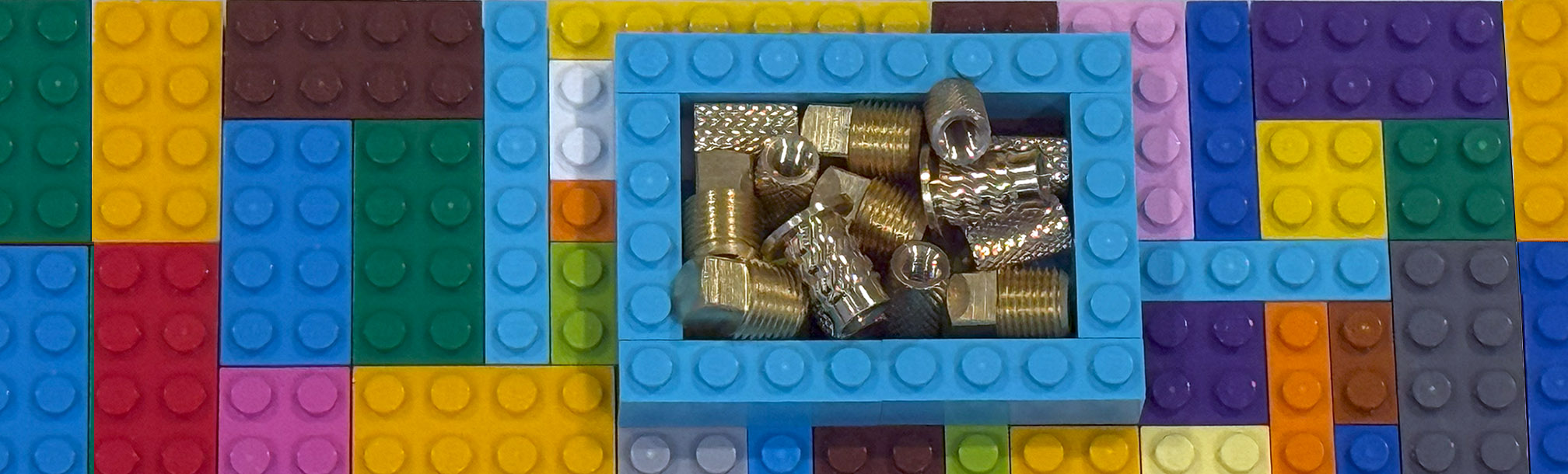
Fasteners used with plastics and composites are subjected to different forces than ones used in metals and other materials. Plastics respond in a completely different manner than metals when subjected to mechanical loads. They exhibit behaviors such as creep, anisotropy, and variable tensile strength depending on polymer type and fiber orientation. To design production-ready assemblies, engineers must understand how mechanical stress is distributed in and around fasteners embedded in plastics and composites – and how these materials react under load-bearing conditions.
Why Stress Distribution Matters
When a fastener is installed into a substrate, it introduces a combination of axial (clamping), radial (expansion) and torsional (driving) forces. These forces are all focused into a small region at the threads and under the head of the fastener.
Metals are able to redistribute these forces effectively due to their stiffness and ductility. Plastics and composites tend to keep these forces concentrated at specific points. These points are generally concentrated around the threads and under the head of the fastener. This concentration of stress is what leads to creep and what increases risk of localized failure.
This stress concentration can result in:
- Cracking and deformation around holes or molded-in bosses
- Thread stripping or pull-out under load
- Creep and permanent deformation over time
- Delamination or fiber damage in composite layers
- Loss of clamping force due to stress relaxation
How do Plastics and Composites Respond to Load-Bearing Connections?
Plastics: Viscoelasticity and Creep
Plastics are viscoelastic materials, meaning they exhibit both elastic (spring-like) and viscous (flow-like) behavior under load. Over time, constant loading—like clamping from a bolt or thread engagement force and compression from a self-tapping screw— can lead to a slow, permanent deformation that compromises joint integrity, better known as creep.
Creep can be pronounced in thermoplastics such as ABS, nylon, or polypropylene. Over-tightening a fastener may initially feel secure, but the material can flow over time, leading to loosened joints or structural instability.
Composites: Anisotropy and Delamination
Creep may be less of a concern with high-stiffness composite materials like carbon fiber-reinforced polymers, they are other issues to contend with. These materials offer exceptional strength-to-weight ratios – meeting, and sometimes even exceeding steel, titanium and other metals. However, because these composites are anisotropic, stiffness and strength vary based upon fiber orientation.
When fasteners are introduced:
- Load transfers unevenly, depending on fiber orientation
- Delamination may occur between composite layers, especially with through-bolts
- Fiber cracking or matrix failure can initiate from high stress points at the fastener interface
Proper load-bearing connection design in composites often requires load-spreading hardware, bonded inserts, or specialized fasteners designed for low-stress introduction.
What Fastener Design Techniques are used to Improve Stress Distribution?
To remove the risk of potential joint failure in plastics and composites, there are several types of components and fasteners that can be deployed. Bear in mind that fastener type may be dependent upon other factors beyond composite performance including cost, weight, and type of metal.
1. Threaded Inserts
Threaded inserts—particularly heat-set or molded-in types—help distribute load more evenly by taking the load off of the substrate and moving it to the insert itself. Inserts also have the benefit of allowing for repeated assembly/disassembly without wear in thermoplastics.
2. Load-Spreading Hardware
Using flanged fasteners or washers increases surface area under the fastener head. This lowers the compressive stress on the plastic or composite surface.
3. Boss and Hole Design
An insert boss (a reinforced cylindrical feature around the hole) can dramatically improve a substrate’s load distribution. A well-designed boss enhances the strength of the joint by optimizing dimensions such as outer diameter, wall thickness, and thread engagement depth—helping prevent cracking or thread pull-out.
Final Thoughts
Designing fastening solutions for plastics and composites is not just a matter of choosing a screw and torque value. It’s a structural engineering challenge that requires a partnership between engineers at both the substrate and fastener level. Understanding how these plastics and composites behave under load—including how joints behave as materials approach their failure limits—is vital to ensuring joint integrity and long-term performance.
With sound design and a strong understanding of material behavior, engineers can create joints that remain reliable—even under demanding conditions.
Where does CFI fit in?
For over 30 years, Components for Industry has been a worldwide provider in industrial components and a partner for industrial plastics and composites companies in a number of industries such as Automotive, Aerospace, Appliance and Heavy Industrial. If you want more information about CFI, our industrial components or our custom design process, contact us at 847-918-0333 or sales@componentsforindustry.com
Sources
- Seymour, R.B. & Carraher, C.E. Introduction to Plastics Engineering. Springer, 2020.
- Bray, A. & Woodward, P. Mechanical Fastening of Plastics: An Engineering Handbook. Springer, 1996.
- Blake, A. The Mechanics of Threaded Fasteners and Bolted Joints for Engineering and Design. Marcel Dekker Inc., 1985.