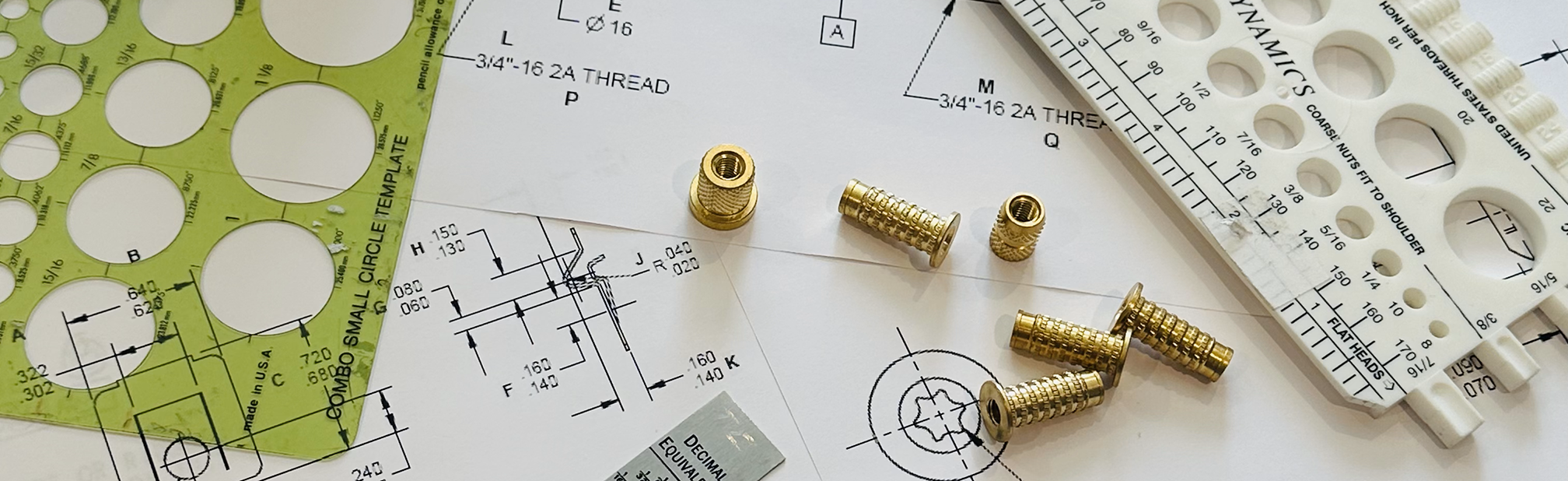
Boosting precision while reducing production costs: The role of threaded inserts in aerospace manufacturing
In the aerospace industry, precision, durability, and efficiency are critical in every aspect of design and assembly. Threaded inserts play a significant role in meeting these demands by helping streamline the assembly process while ensuring structural integrity in high-stress environments. In this blog, we’ll explore how aerospace engineers leverage components like threaded inserts to increase assembly efficiency, reduce production costs, and enhance performance in advanced aerospace applications.
Simplifying Assembly in Lightweight Materials
Weight comes at a premium in aircraft and spacecraft. As a result, aerospace engineers often work with lightweight materials like aluminum, carbon fiber composites, and various plastics. These materials, while ideal for reducing fuel consumption and increasing payload capacity, often lack the strength required to hold screws or bolts directly. Traditional fastening methods with these materials would lead to material damage, stripping of threads, or structural weaknesses.
With the use of threaded inserts, engineers can install durable, reusable threads within these relatively soft materials while retaining their desired lack of weight. In addition, the use of inserts would prevent thread deformation and allow for repeated assembly and disassembly without compromising the integrity of the mated components. This not only simplifies the fastening process, but also ensures the long-term reliability in service.
Reducing Assembly Time
Assembly can take up a significant portion of the total cost of manufacturing an airframe due to the labor and quality issues that arise from drilling thousands of holes per aircraft. As a result, efficiency in assembly is absolutely critical in aerospace manufacturing, where every minute saved can result in significant cost savings. Use of threaded inserts can contribute to faster assembly times in several ways:
- Pre-installed inserts: Inserts can be pre-installed in parts before final assembly, allowing technicians to quickly attach components without worrying about alignment or thread quality. This reduces manual labor and decreases the likelihood of errors from manual drilling, use of sealants, reduction of burrs and delamination.
- Elimination of Retapping: When traditional threads wear out, retapping or replacing the entire part is often necessary. Threaded inserts, however, are designed to last much longer than traditional threads drilled directly into a mated material – especially in high-stress environments like extreme temperatures and pressures that aerospace fasteners have to endure. Their use prevents costly delays associated with rethreading damaged holes.
- Automated Assembly Compatibility: Threaded inserts are compatible with automated assembly lines, enabling the use of robotic fastening systems. One of the largest costs of building an airframe is drilling holes – and the cost is so high because of the need for “high hole quality” including uniformity for structural integrity1.
Ensuring Vibration Resistance
Aircraft and spacecraft are constantly exposed to vibration during flight. This constant vibration can cause components like screws and bolts to loosen over time. This issue is especially problematic in systems with complex assemblies, where loose fasteners can lead to component failures or malfunctions.
Threaded inserts offer vibration resistance, especially when paired with self-locking designs. The inserts can create a stronger, more stable connection that is less likely to loosen under vibrations, thus reducing the need for maintenance checks and ensuring that critical components remain securely fastened.
Enhanced Corrosion Resistance
Aerospace components are exposed to extreme conditions. Between extreme temperatures and pressure changes, aerospace components are exposed to moisture, chemicals and other factors that can promote corrosion. Threaded inserts made from materials like stainless steel and brass offer superior corrosion resistance compared to screws threaded directly into softer metals or composites. This would increase the lifespan of both the fastener and the surrounding materials.
Conclusion
Threaded inserts play a vital role in enhancing assembly efficiency across the aerospace industry. From simplifying fastening in lightweight materials to ensuing vibration resistance, these versatile components are essential for improving both the manufacturing and operational phases of aerospace projects.
By incorporating threaded inserts into their designs, aerospace engineers can reduce production costs, speed up assembly processes, and ensure long-lasting, reliable performance.
Where does CFI fit in?
For over 30 years, CFI has been a worldwide provider in industrial components such as brass inserts for a wide number of industries like Automotive, Aerospace, Appliance and Heavy Industrial. If you want more information about CFI, our industrial components or our custom design process, contact us at 847-918-0333 or sales@componentsforindustry.com.
- Latger, F., Harris, T., and Björklund, S., “Drilling Cost Model,” SAE Technical Paper 2002-01-2632, 2002, doi:10.4271/2002-01-2632. ↩︎