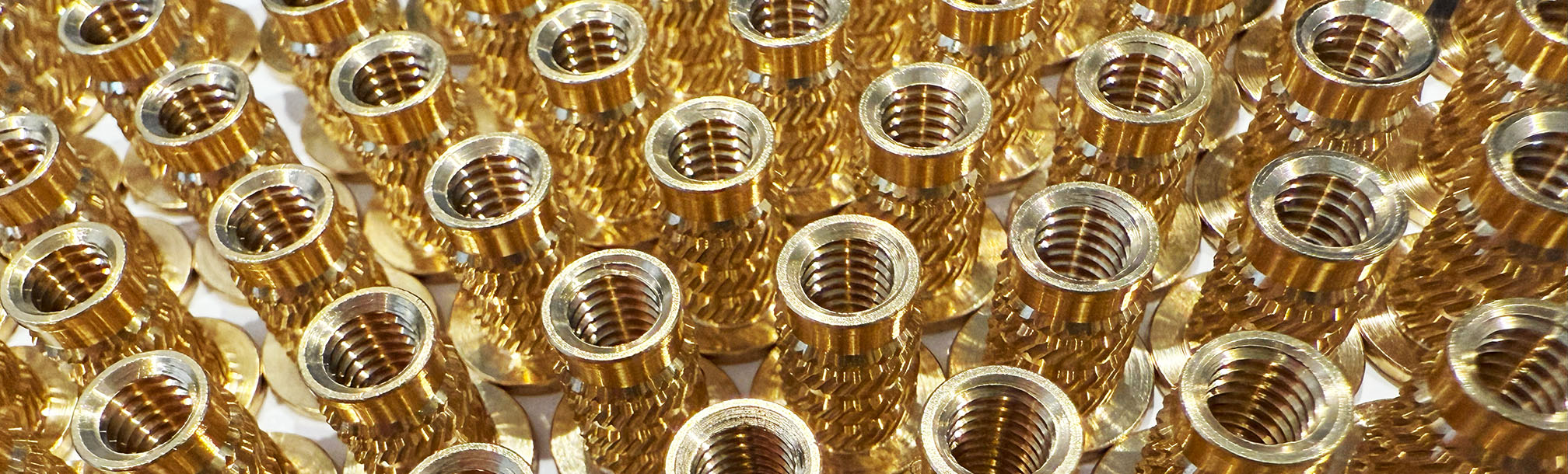
When designing a new product, thousands of seemingly minute engineering decisions turn into the final product. One of the most important decisions is choosing the fastener materials. While it may not sound like a big decision to a layman, it can have a profound downstream effect on the build quality, look, and perhaps most importantly, the cost of your product for the end consumer.
When choosing the perfect fastener material for your project, an engineer starts at five basic criteria: Strength, Corrosion Resistance, Temperature Resistance, Weight, and Cost-Efficiency.
Brass and Bronze
Brass and bronze are both copper-based alloys known for their corrosion resistance, wear resistance, electrical and thermal conductivity. Brass is an alloy made from copper and zinc; while bronze is made from copper and tin.
Brass and Bronze Material Strengths
Thanks to the copper content they both have an attractive reddish-gold color, making them both useful in luxury hardware. In addition, their corrosion resistance suits marine hardware, wear resistance benefits industrial machinery, and conductivity aids electrical connectors and architectural applications.
Brass and Bronze Weaknesses
Brass and Bronze are softer than steel, with a Brinell Hardness of around 60 for Soft Brass1 (depending on the zinc content and alloy composition). It is, however, harder than aluminum. In addition, it is generally more expensive than either steel or aluminum, which can be a limitation for large-scale projects. Additionally, a unit of brass and bronze is also heavier than aluminum, titanium and even steel.
Brass and Bronze Applications
Thanks to their copper content, both metals feature an attractive reddish-gold color, making them popular in luxury hardware. You can see brass and bronze nuts, bolts and screws alongside drawer pulls, light fixtures and even parts in luxury cars, boats and airplanes. Beyond appearance, thanks to its conductivity, you will find brass and bronze components in switches and connectors.
Steel
Steel is one of the most popular fastener materials and comes in a large variety of forms and strengths such as alloy steel, carbon steel, stainless steel, and many more. Steel’s corrosion resistance and mechanical strength make it an attractive option for many product designers looking for the perfect fastener.
The Brinnel Hardness number of even mild steel more than doubles that of bronze, coming in at 130 BHN1. Meanwhile, carbon steel fasteners are known for their exceptional strength, ranging in value between 163-6002. Finally, the heat resistance of steel fasteners is second-to-none with max useable temperatures ranging from 400 to 1,100 degrees3 Celsius and a melting point of 1510 – quadrupling the max usable temperatures of Aluminum.
Steel Strengths
Steel, Carbon Steel, Stainless Steel, et al fasteners are known for their tensile strength. This strength makes them ideal for structural and high-load applications. In addition, with the right coating, such as zinc (for corrosion protection and aesthetic appeal) and phosphate (for wear reduction and lubricant adhesion in high-friction environments), steel can make up for some of its relative shortcomings compared to brass and aluminum.
As the most widely-used fastener material in the world, cost is not an issue with steel components. Its ubiquity has made it inexpensive compared to brass, aluminum, titanium and other, more exotic materials.
Steel Weaknesses
Corrosion. Steel would not need phosphate and zinc if it weren’t so susceptible to rust and corrosion – especially in humid or marine environments. In addition, it is heavier than Aluminum, Titanium, but is actually lighter than brass and bronze.
Steel Applications
Due to the material’s strength, steel fasteners are used in a wide variety of industries, from construction to automotive to aerospace and more. Stainless is used in the aerospace and marine industries where corrosion resistance and strength are critical and where untreated steels may come up short.
Aluminum
Aluminum has become a good all-around alternative for fasteners because of its light weight and high corrosion resistance. In addition, if combined with other metal alloys, some aluminum alloys such as 70754, can actually rival mild steel’s strength for a fraction of the weight. This makes some aluminum alloys an ideal option for automotive and aerospace components where weight and strength are of utmost importance.
Aluminum Strengths
Aluminum fasteners are significantly lighter than either steel or brass, making them ideal for weight-sensitive applications. In addition, aluminum is corrosion-resistant, only forming a natural oxide layer in lieu of rust, protecting it from corrosion in most environments.
Aluminum is also non-magnetic, making it ideal for electronic manufacturing, medical devices, aerospace, and more where magnetic interference can interfere with precision instrumentation. Finally, aluminum allows for extremely intricate designs and custom threading.
Aluminum Weaknesses
With the exception of select alloys, aluminum is generally softer and weaker than carbon and stainless steel fasteners and inserts. However, with heat treatments, it can have very hardness that can rival some steels. In addition, high-grade aluminum alloys are also more costly than standard steel and can be harder to form than other metals. Finally, while aluminum does allow for intricate designs, it must be done with specific machinery, making it a unique metal to work with.
Aluminum Applications
Due to the relatively high tensile strength to weight ratio of select aluminum alloys, you will see aluminum fasteners heavily deployed in the Aerospace, Aviation, Marine, and Automotive industries. In essence, wherever maximum strength at minimum weight are championed, aluminum alloys are used.
Titanium
In the last few decades, Titanium has been considered a somewhat exotic material thanks to its high strength to weight ratio and other properties. To place that into perspective, the softest commercially pure titanium has a Brinell Hardness Number of ~120; while medical grade titanium can have BHNs of ~320, placing it on par with various steels. In addition, it is non-magnetic, has a relatively high maximum useable temperature range of around 600° – 800° Celsius. As incredible as titanium components are, they are expensive compared to their brass, steel and aluminum counterparts.
Titanium Strengths
Titanium has a number of attractive properties going for it that make it worth its premium cost and relatively low availability:
- High corrosion resistance
- Exceptional strength compared to its weight
- Moderately high temperature resistance
- Non-magnetic
- Non-toxic and compatible with the human body
Titanium Weaknesses
While titanium isn’t exactly rare, it is expensive to extract, purify and machine; requiring high temperatures and specialized tools. All of this leads to higher costs of the end products including components. In addition, titanium components can be affected by supply chain issues because of the base material’s availability.
Titanium Applications
Titanium’s light weight, temperature tolerance and biocompatibility has made it an ideal fastener material for aerospace, marine, high performance automotive and medical. Like aluminum, it is also non-magnetic, again making it an ideal candidate for aerospace because it does not interfere with precision instruments. However, it has a higher tolerance for temperatures, making it a better candidate for higher wear applications.
Heat Sensitivity
When choosing materials for your project’s fasteners, heat sensitivity is a major concern. A base material’s melting point would be the logical number to look at, however, it tells an incomplete story when choosing fasteners. Why? It’s because an engineer needs to take into account when a material loses its mechanical and structural properties – not just its melting point.
The first chart tells us when the fastener metals melt; the second tells the story of when the temperature begins to affect their performance.
Melting Point (Celcius) | ||
Material | Melting Point (Celcius) | Key Properties |
Carbon Steel | ~1410-1540 | |
Aluminum Alloys | ~500-630 | |
Pure Titanium | ~600 | Ideal for high-stress, high temperature environments |
Pure Aluminum | ~660 | Mechanical Properties degrade above 200°C |
Titanium Alloys | ~800 | See Titanium |
Brass | ~930-1050 | Prone to creep at high temperatures, corrosion resistant |
Stainless Steel | ~1510 | High-strength, heat resistant due to chromium content |
It’s this latter chart that is more important when considering component materials. In addition, when considering materials like titanium, cost becomes a concern, unless weight and heat resistance is of paramount importance such as aerospace applications.
Max Usable Temperature | ||
Material | Max Useable Temp (Celcius) | Weaknesses |
Aluminum | 200-250 | Low Heat Tolerance |
Brass | 300-400 | Moderate Heat Tolerance |
Titanium | 600-800 | High cost compared to alternatives |
Steel | 400-1100 | Heavy compared to alternatives |
Conclusion
Each fastener material – brass, steel, aluminum, and titanium – has its own unique set of strengths and weaknesses, as well as its own applications. By understanding how theses materials perform in different conditions, engineers can make informed decisions about the best fastener materials for their designs, ensuring the perfect balance between cost, strength and performance.
Where does CFI fit in?
For over 30 years, Components for Industry has been a worldwide provider in industrial components such as steel, aluminum, brass and titanium industrial fasteners for a wide number of industries like Automotive, Aerospace, Appliance and Heavy Industrial. If you want more information about CFI, our industrial components, our brass inserts, or our custom design process, contact us at 847-918-0333 or sales@componentsforindustry.com.
- The Engineering Toolbox. Brinell Hardness Number – BHN. Obtained from: https://www.engineeringtoolbox.com/bhn-brinell-hardness-number-d_1365.html ↩︎
- Overview of materials for High Carbon Steel. MatWeb – Material Property Data. Obtained from: https://www.matweb.com/search/datasheet_print.aspx?matguid=ee25302df4b34404b21ad67f8a83e858 ↩︎
- Stainless Steel – High Temperature Resistance. Azo Materials. Obtained from: https://www.azom.com/article.aspx?ArticleID=1175 ↩︎
- Henning, A. 7075 vs. 6061 Aluminum Choosing the Right Alloy for Performance. Tech Steel & Materials. Obtained from: https://www.techsteel.net/7075-vs-6061-aluminum-choosing-the-right-alloy-for-performance#:~:text=6061%20Aluminum%20Alloy%20is%20significantly,Aerospace%20aan%20Aviation%20Uses ↩︎