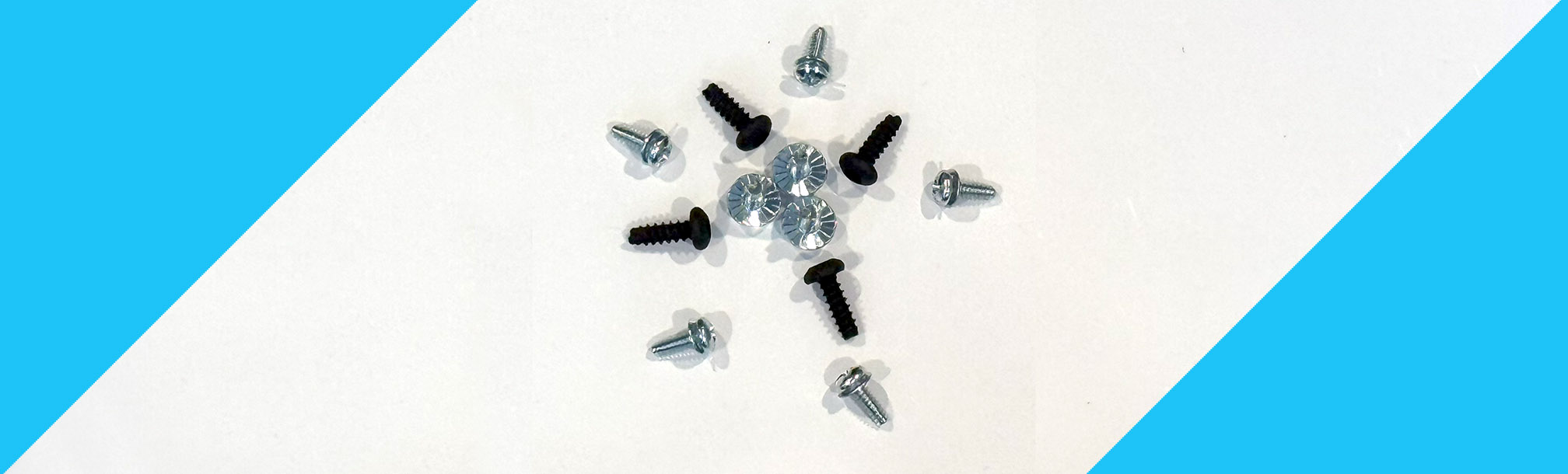
Selecting the coating of a fastener is one of the first and most important decisions that an engineer must make. When making this decision, engineers must consider a myriad of important decisions. These decisions include: environmental conditions, corrosion resistance, temperature resistance, electrical conductivity, durability, and of course, cost of the chosen finish.
Two of the most widely used treatments in industrial applications are zinc and phosphate coatings, particularly in the automotive, aerospace, construction, and heavy machinery sectors. Understanding the strengths and weaknesses of these fastener coatings is essential for ensuring optimal performance and cost-effectiveness.
What factors influence fastener coating selection?
When choosing the correct fastener finish, consider factors such as Embrittlement Protection, Corrosion Protection, Resistance to Handling Damage, Criticality of the Joint, Functionality, Cost, and Availability.
Hydrogen Embrittlement Protection – The electroplating process uses a bath made up of water, dissolved metal salts, ions, and other chemicals. If the fastener coating process is not properly controlled, it can lead to excess hydrogen absorption. This excess hydrogen reduces ductility, weakens load-bearing capacity and increases the risk of cracking or failure from stress. To mitigate these potential issues, the component is baked immediately after plating to diffuse absorbed hydrogen atoms and restore material integrity.
Corrosion Protection – A finish’s resistance to corrosion in its operating environment is a key consideration for end users. Typical protective measures include lacquers, plating, and coatings. These are all deployed to create a protective layer from corrosion. However, a fastener might require a more robust coating if it is regularly exposed to moisture, saline solutions, temperature changes, or physical wear from collisions. Examples of more robust coatings could include zinc-nickel coatings, hot-dip galvanizing and phosphate coatings.
Criticality of the Joint: Certain coatings, while they may offer benefits in aesthetics or corrosion resistance, can also affect friction. This can potentially hinder critical fastener applications. Engineers must consider the impact a loose joint has on the overall assembly. Some finishes lack reliable friction values, making them unsuitable for fasteners in applications that require consistent and repeatable clamp loads.
Functionality: For fasteners with small diameters, fine threads, or internal recess drives, an improper finish can lead to excess coating buildup, potentially interfering with proper engagement and performance.
Cost and Availability: Specialized coatings can significantly increase both the fastener price and overall production costs. Additionally, some finishes may require special ordering due to their limited availability. This may lead to longer lead times and higher expenses.
Zinc vs. Phosphate Coatings
Zinc Coatings: Sacrificial Corrosion Protection
Zinc Coatings, applied through electroplating and hot-dip galvanizing, protects metal components by providing a sacrificial layer where the zinc corrodes instead of the base metal. This sacrificial layer prevents rust formation on fasteners and other components, extending the lifespan.
Industrial Applications for Zinc Coatings
- Automotive: Zinc-coated fasteners are extensively used in car frames, chassis components, and suspension systems due to their ability to withstand road salt and moisture exposure.
- Construction: Steel structures, roofing screws, and exterior fasteners utilize zinc coatings to reduce rust formation and extend service life in outdoor environments.
- Heavy Equipment: Tractors, bulldozers, and industrial machinery benefit from zinc plating to reduce maintenance costs and extend service life.
Advantages of Zinc Coatings
- Excellent corrosion resistance, especially in atmospheric conditions
- Self-healing properties due to the sacrificial nature of zinc where the zinc corrodes before the base metal
- Cost-effective solution for general-purpose and outdoor applications
Limitations of Zinc Coatings
- Prone to white rust (zinc oxide formation) in high-humidity environments
- Limited wear resistance compared to phosphate or harder coatings
- May require additional passivation or sealer treatments (such as chromate conversion coatings) for enhanced durability
Phosphate Coatings: Enhanced Paint Adhesion and Wear Resistance
Unlike Zinc Coatings, which provide a sacrificial layer, Phosphate Coatings protect base metals by forming a barrier against corrosive elements. Common types of Phosphate Coatings include zinc phosphate and manganese phosphate, both of which create a crystalline structure on the metal surface. This crystalline structure improve paint adhesion, enhances lubricant retention and provides moderate wear resistance, making phosphate coatings ideal for components that require further processing or finishing.
Industrial Applications for Phosphate Coatings
- Aerospace: Aircraft fasteners and structural components use phosphate coatings as a primer for additional protective layers, ensuring resistance to extreme temperature fluctuations.
- Heavy Equipment: Phosphate-coated bolts, nuts, and washers in tractors, bulldozers, and other industrial machinery help reduce galling and improve service life.
- Manufacturing and Machinery: Machine parts, gears, and industrial tools benefit from phosphate coatings due to their ability to retain lubricants and reduce friction, reducing wear during use.
Advantages of Phosphate Coatings
- Superior adhesion for paint, powder coatings, and lubricants
- Enhanced wear resistance; making them ideal for moving parts in motors and other high-friction parts
- Effective pretreatment for metal forming and stamping operations
Limitations of Phosphate Coatings
- Lower standalone corrosion resistance compared to zinc coatings
- Requires additional sealing or painting for long-term durability
- More complex application process compared to zinc plating
Conclusion
Both zinc and phosphate coatings provide distinct advantages for industrial fasteners and components, making them suitable for different applications in industrial settings. Zinc coatings are ideal when corrosion resistance is the primary concern, particularly in outdoor and high-moisture environments such as construction, automotive, and heavy equipment industries. In contrast, phosphate coatings excel in applications requiring enhanced wear resistance, lubricant retention, and strong paint adhesion, making them a preferred choice for manufacturing, aerospace, and metal-forming processes.
By evaluating environmental exposure, mechanical stress, and durability requirements, engineers can select the most effective coating for their fasteners and industrial components, ensuring long-lasting performance in demanding conditions.
Where does CFI fit in?
For over 30 years, Components for Industry has been a worldwide provider in industrial components such as zinc and phosphate industrial fasteners for a wide number of industries like Automotive, Aerospace, Appliance and Heavy Industrial. If you want more information about CFI, our industrial components or our custom design process, contact us at 847-918-0333 or sales@componentsforindustry.com.