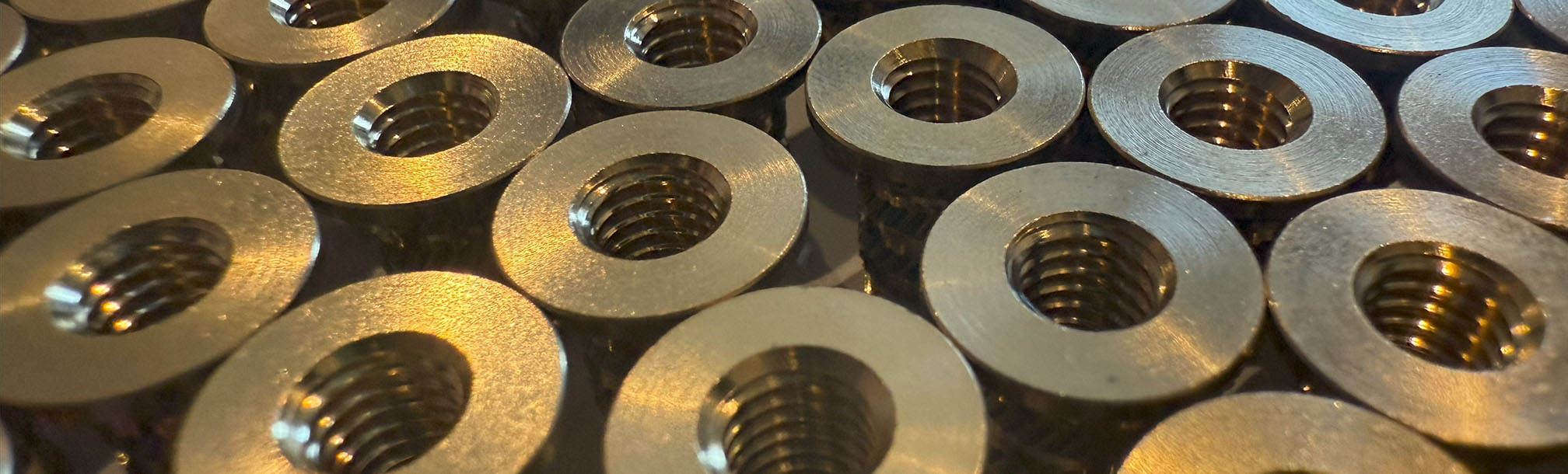
Threaded inserts are essential in any industry where strong connections are needed, enhancing durability, design flexibility, and load-bearing capacity. Now, the need for the threaded insert is unquestioned. The hard part is deciding the material for the insert. Why? It’s because there are pros and cons for every common threaded insert material.
What are the most common threaded insert materials?
Before we get into specifics, let’s look at the most widely-used materials: Brass, Steel and Aluminum. Then we will look at the pros and cons of each material.
Engineers use brass inserts the most often amongst the three materials. It is known for its corrosion resistance, machinability, cost effectiveness, thermal conductivity, and electrical conductivity. It is an alloy of copper and zinc, with small amounts of lead for better machinability.
Steel, more specifically, stainless steel and carbon steels are both known for their strength, and durability. Steel is relatively cost-effective, offering better affordability than brass, despite brass being easier to machine due to its higher material costs. Both carbon and stainless steels are also known for being highly resistant to corrosion and wear.
Aluminum is utilized for its lightweight properties and is also non-magnetic, making it ideal for applications where weight is critical such as aerospace applications. In addition, it is also easier to machine than steel, but lacks the cost-effectiveness of steel. In addition, it is the weakest of the three threaded insert materials.
What are the pros and cons of brass inserts?
Brass inserts are commonly used in applications where corrosion resistance, conductivity, and ease of installation are all important factors. Common uses are electrical components, plumbing fixtures, and marine hardware. You can find brass inserts used in appliance, automotive, electronics, aerospace, HVAC, marine, telecommunications, and many other industries.
Brass inserts are popular due to their machinability and corrosion resistance. They are non-magnetic, thermally conductive, resistant to wear, and electrically conductive, making them ideal for use for use in electronics and automotive parts.
However, brass can be more expensive than both steel and aluminum, which can increase project costs. Finally, while brass is stronger than aluminum, there are strength limitations compared to steel inserts. Essentially, brass is in the goldilocks zone in terms of strength, corrosion resistance and price coefficient for many industrial purposes. That is why many companies choose brass inserts over threaded inserts made from other materials.
What are the pros and cons of steel inserts?
Steel inserts are typically chosen by engineers and product designers due to their hardness, strength, and relative lack of cost due to the material’s ubiquity. Steel’s 800-year history has allowed engineers to perfect its strength and reliability. That’s why steel inserts are chosen for high-stress applications where the threaded insert has to withstand significant mechanical loads. This strength makes steel threaded inserts ideal where the threads require repeated use – such as applications with repeated installation of screws or bolts that would otherwise deform inserts made from softer materials such as brass or aluminum.
Now, with that hardness and strength come some drawbacks. Inserts made from standard carbon steels are prone to rust and corrosion – unless they are treated with protective coatings or used in controlled environments. In addition, the hardness of steel can lead to wear on softer surrounding materials, such as plastics or composites during installation.
What are the pros and cons of aluminum inserts?
Aluminum’s lightweight, non-magnetic and anti-corrosion properties have made it an attractive option in the automotive and aerospace industries for as long as those sectors have existed. Aluminum first came into industrial use in the early 20th century as a lightweight, corrosion-resistant alloy. The material was deployed in some of the very first cars and airplanes such as the 1915 Junkers J1’s aluminum fuselage and the 1899 Durkopp luxury automobile’s aluminum body panels.
The pros of the lack of weight and corrosion resistance carry through to threaded inserts. In addition, aluminum inserts have the added benefit of thermal conductivity. This makes them suitable for applications where heat dissipation is important, such as engine components. In addition, aluminum is remarkably easy to machine, reducing manufacturing costs. Aluminum’s recyclability makes it ideal for industries prioritizing sustainability and net-zero goals.
As for the cons of aluminum, aluminum is generally two to three times more expensive than carbon steel per unit weight, depending on market conditions. In addition, most aluminum alloys have lower fatigue strength and are softer than steel and brass alloys, making them less resistant to wear, and therefore potentially prone to thread stripping after repeated use. Finally, aluminum has a high coefficient of thermal expansion. This can lead to loosening or misalignment in applications involving significant temperature fluctuations.
How do you choose the right material for your threaded inserts?
When selecting the right threaded insert material, the decision ultimately depends on the specific needs of your application. Brass offers a balance of machinability, corrosion resistance, and conductivity, making it ideal for electronics and marine hardware. Steel provides unmatched strength and durability for high-stress environments, while aluminum’s lightweight and thermal conductivity excel in weight-sensitive industries like aerospace and automotive. Each material has its distinct advantages and trade-offs, so understanding the requirements of your project will help you make an informed choice. By evaluating these factors, you can ensure your threaded inserts perform reliably and efficiently in their intended application.
Where does CFI fit in?
For over 30 years, CFI has been a worldwide provider in industrial components such as threaded inserts for a wide number of industries like Automotive, Aerospace, Appliance and Heavy Industrial. If you want more information about CFI, our industrial components or our custom design process, contact us at 847-918-0333 or sales@componentsforindustry.com.