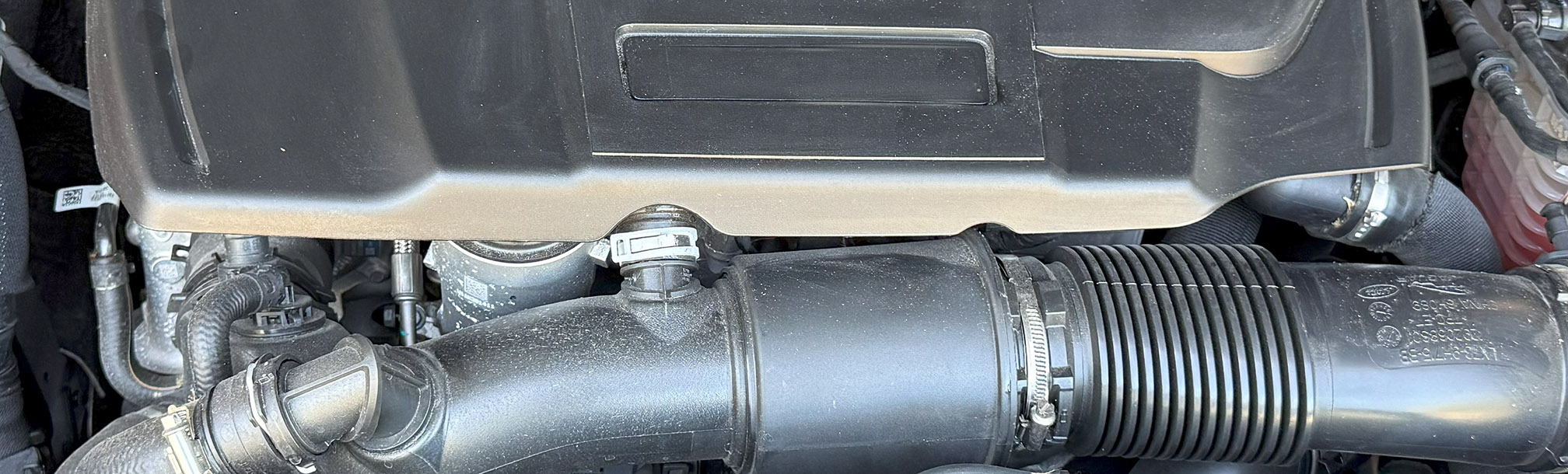
Noise, Vibration and Harshness (NVH) has long been a critical metric for buyers when deciding the overall quality of a vehicle. That’s why we, as fastener and plastics engineers, have to begin thinking about NVH quite literally at the nuts and bolts level.
Whether you’re talking about EVs or traditional internal combustion engine (ICE) platforms, NVH plays a major factor – but in different ways. For EVs, it’s all about silence and refinement; for ICE vehicles, it’s about masking engine vibrations and managing harmonics. Across both types of platforms, issues can begin at mechanical joints between plastics and fasteners.
As OEMs continue to integrate more composites and plastics for weight reduction and complex geometries, the fastener interface becomes a primary NVH contributor. Without early collaboration between plastics and fastener engineers, these joints may become unintended sources of buzzing, rattling, or harmonic amplification—especially under thermal, vibrational, and assembly loads.
Where NVH Starts: The Joint Interface
Whether it’s a dashboard bracket, powertrain cover, or underbody sensor mount, NVH failures frequently stem from:
- Micro-movement between fasteners and plastic bosses
- Differential thermal expansion between metal fasteners and plastic substrates
- Stress relaxation and creep in plastics under clamping force
- Underdamped assemblies transmitting engine or road vibrations
While these issues can affect both EV and ICE architectures, the nature of the NVH challenge varies by propulsion system:
- EVs are quieter by nature, making even subtle vibrations and component chatter noticeable to the driver.
- In ICE vehicles, NVH management focus changes to combustion-induced harmonics and vibration prevention
Why Plastics and Fastener Engineers Must Collaborate Early
NVH mitigation is not solely the job of acoustics specialists. Instead, the interaction between fasteners and plastic parts must be engineered from the outset. Co-designing joints with input from both disciplines enables:
1. Reduced Vibratory Transmission
- Using thread-forming fasteners specifically designed for plastics to minimize hoop stress
- Incorporating damping materials, isolator washers, or floating inserts to absorb vibratory energy
- Avoiding metal-on-metal contact where practical, especially in interior or structural assemblies
2. Thermal and Mechanical Compliance
- Selecting inserts that accommodate thermal cycling without inducing loosening
- Tuning clamp loads based on plastic relaxation curves and service temperature range
- Designing joint geometries that account for expansion mismatch between plastic and steel
3. Assembly Robustness Under Real-World Loads
- Preventing over-torque during line assembly, which can deform plastic bosses or alter vibratory behavior
- Using self-aligning or compliant fastener features to maintain consistent preloads across manufacturing variance
- Leveraging joint simulations and FEA to visualize NVH risks during design reviews
NVH in Prototyping: Fastener Decisions Matter Early
At the prototyping stage, OEM engineering teams often focus on structural validation—yet NVH behavior can be locked in or lost at this point. Joint-level NVH evaluations that include fastener/plastic interactions help:
- Identify critical buzz or rattle points under simulated road load conditions
- Tune material stack-ups (plastic, isolator, fastener) before design freeze
- Validate compliance with brand-specific NVH thresholds and target spectra
This is particularly true in dashboard assemblies, HVAC enclosures, battery pack interfaces, and engine covers, where both airborne and structure-borne noise sources are highly sensitive to joint quality.
Applications Across ICE and EV Platforms
While EVs and ICEs present different acoustic environments, both share common high-risk areas for fastener-induced NVH:
Application | EV Considerations | ICE Considerations |
Instrument Panels | Low ambient noise → squeak/rattle detection | Combustion masking helps but requires durable joints |
Underhood Plastic Covers | Must handle vibration from road & drivetrain | Engine vibration adds thermal + harmonic complexity |
Battery Enclosures | Isolate harmonics, manage expansion joints | N/A |
Air Intake & Cooling Ducts | Mount stability under fan & airflow vibration | Vibration harmonics from engine components |
Interior Brackets & Trims | Friction noise, rattling from occupant interaction | Same, with additional masking from engine sound |
Summary: NVH Risk Is a System Problem, Solved at the Component Level
Effective NVH reduction requires cross-functional engineering collaboration. When plastics and fastener experts work in silos, the result is often an acoustically unpredictable joint. But by collaborating during design, prototyping, and validation, OEMs can proactively engineer quieter, more robust assemblies across EV and ICE platforms alike.
Final Thoughts
Whether your vehicle is driven by electrons or gasoline, NVH failures at plastic-fastener interfaces can derail performance and perception. The solution isn’t just testing—it’s co-designing. By aligning fastener selection, joint geometry, and material behavior early in the development process, engineering teams can systematically reduce noise sources, streamline validation, and build higher-performing vehicles from the inside out.
Working on a platform where NVH is critical?
Components for Industry (CFI) collaborates with plastics suppliers, Tier 1s, and Automotive OEM design teams to optimize fastening strategies for NVH performance—before they reach the validation stage.