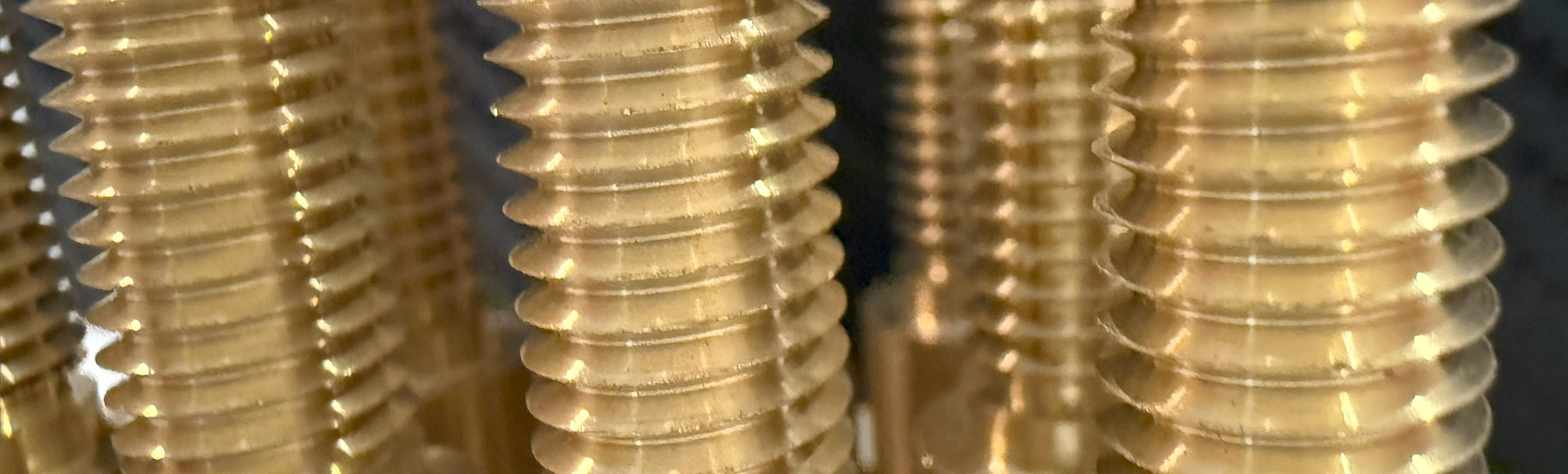
Choosing the right bolt means knowing how it fails and when it bends too far to bounce back
When designing or specifying fasteners, strength is everything, but not all strength is created equal. Two key properties – yield strength and tensile strength – tell very different stories about how a bolt behaves under load. If misunderstood, they can lead to catastrophic failure, excessive deformation, or simply a bolt that doesn’t do its job.
In this post, we’ll break down what each term means, why both matter in bolt selection, and how to use them together to make smarter design decisions, particularly in applications involving plastics and composites.
What Is Yield Strength?
Yield strength is the amount of stress a bolt can withstand before it permanently deforms. In other words, it’s the stress level at which a material stops behaving elastically (bouncing back) and starts to stretch permanently, even if the load is removed.
Think of it as the point where a bolt “gives” but doesn’t break.
Why Yield Strength Matters:
- Bolts function by creating clamping force – this comes from stretching the bolt slightly like a spring.
- If you exceed yield strength, the bolt no longer behaves like a spring.
- This results in loss of preload, reduced clamping force, and ultimately joint failure – even if the bolt doesn’t break.
In fact, most properly torqued bolts are loaded to 70–90% of their yield strength, allowing maximum clamping without entering permanent deformation and potential thread failure is deliberately built into the nut.
What Is Tensile Strength?
Tensile strength, or ultimate tensile strength (UTS), is the maximum stress a material can take before it breaks. This is the upper limit of the material’s capacity to withstand stretching.
Once you exceed tensile strength, the bolt will fail, typically by fracturing.
Tensile strength is the number often printed on a bolt’s spec sheet (e.g., 120,000 psi for Grade 5). But it’s not the whole picture.
Why Tensile Strength Matters:
- It defines the absolute maximum capacity of the fastener.
- It’s useful for evaluating overload conditions or determining safety margins.
- It’s a key factor in fastener grades, like SAE Grade 5, 8, or Metric 10.9, 12.9.
Yield vs. Tensile: What’s the Difference?
Here’s a visual comparison of a stress-strain curve (as described in Mechanical Fastening of Plastics):
Point | What Happens | What It Means |
Elastic Region | Bolt stretches and returns to shape | Safe clamping zone |
Yield Point | Bolt starts to deform permanently | Preload loss risk begins |
Plastic Region | Bolt stretches more with less added force | Dangerous, but still intact |
Tensile Strength | Bolt breaks | Catastrophic failure |
The key takeaway:
Don’t design fasteners to operate near their tensile strength. Design them to stay within the yield limit.
Common Fastener Grades and Strengths
Here’s a comparison of common imperial and metric bolt grades, and how their yield and tensile strengths relate:
Medium Carbon Steel, Heat Treated, Quenched and Tempered | |||
Bolt Grade | Nominal Size | Yield Strength | Tensile Strength |
Diameter Inches | Min psi | Min psi | |
2 | 1/4″ – 3/4″ | 57,000 | 74,000 |
2 | 3/4″ – 1 1/2″ | 36,000 | 60,000 |
5 | 1/4″ – 1″ | 92,000 | 120,000 |
5 | 1″ – 1 1/2″ | 105,000 | 81,000 |
5.1 | No. 4 – 5/8″ | – | 120,000 |
5.2 | 1/4 – 1″ | 92,000 | 120,000 |
8 | 1/4 – 1 1/2″ | 130,000 | 150,000 |
8.1 | 1/4 – 1 1/2″ | 130,000 | 150,000 |
8.2 | 1/4 – 1 1/2″ | 130,000 | 150,000 |
In general, yield strength is about 75–90% of tensile strength depending on material and treatment.
Implications for Design in Plastics and Composites
When working with injection-molded plastics, thermoplastics, or fiber-reinforced composites, you’re often clamping into or around low-modulus materials. That means:
- Over-tightening a bolt can crush or creep the plastic
- The clamping force must be precisely controlled
- Choosing a high-strength fastener without considering the yield limit of the substrate can lead to localized deformation or insert pullout
Fastener preload must often be tailored to avoid surpassing the compressive yield strength of the plastic, not just the fastener’s own limit.
Best Practices for Engineers
✅ Design to Yield, Not Ultimate Strength
Use 75–90% of yield strength as your torque limit, not tensile strength.
✅ Consider the Whole System
Fastener strength must be matched to the materials being joined, not just the loading conditions.
✅ Use Threaded Inserts or Load Spreading Features
In composites, preload is limited by the substrate but not the bolt. Use brass or steel inserts, wide flanges, or shoulder screws to spread load and reduce localized stress.
✅ Avoid Over-Engineering
A stronger bolt isn’t always better. You risk damaging the joint or threads, especially in plastic bosses or thin laminates.
Need help choosing the right bolt for a plastic or composite assembly?
Our team at Components for Industry is ready to help you spec fasteners that keep your designs strong and your service life long.
📩 Contact CFI for fastener advice or application-specific solutions.