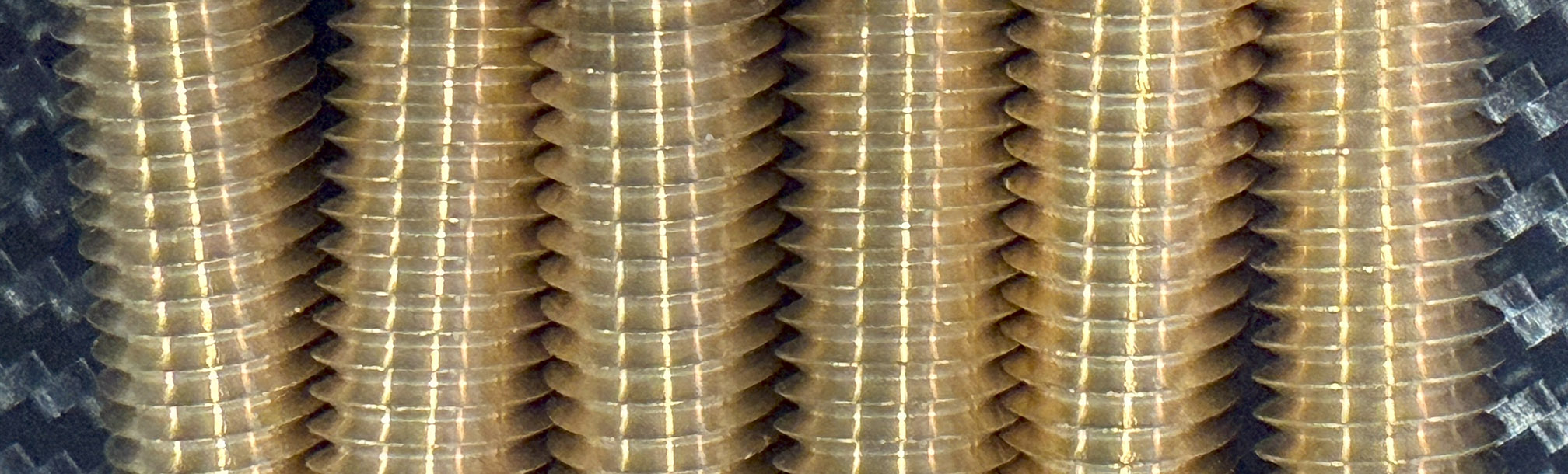
Selecting the Optimal Threaded Insert Seating Method for Industrial Applications
If your plastic or composite assemblies require more strength, heat-set and ultrasonic inserts may be the answer. Heat-Set and Ultrasonic Inserts offer and require more pull-out strength than even traditional press-in inserts. Both of these inserts find their strength by melting the plastic around the insert’s barbs and knurls, seating them into place.
While their final installation might work the same way in theory – embedding the threaded insert in temporarily liquified plastic – which is the better method for your industrial setting? In order to answer this question, we must consider cycle time and how best to minimize defects because these methods differ significantly in process, tooling cost and material compatibility.
🔧 Heat-Set Insertion in Industrial Settings
How it works:
Heat-Set works when a heated tip or press is pressed into a pre-molded or pre-drilled hole. The tip or press then melts the substrate locally, and as the plastic flows around the barbs and knurls, it undercuts the insert, locking it into place as the substrate cools.
🧰 Heat-Set Required Equipment:
- Thermal Insertion Presses to accurately control temperature in industrial settings
- Insertion Tip custom-matched to threaded inserts
- Jigs to hold plastic assemblies in place
- Temperature Controllers to maintain stable heat at tip
- Fume Extraction Systems to remove fumes for plastics like ABS and PVC
✅ Advantages:
- Lower equipment costs than comparable ultrasonic systems
- Strong mechanical retention in materials like ABS, PC, and PA6
- Gentle on brittle plastics, reducing stress cracks and distortion
Heat staking is particularly useful when working with semi-crystalline thermoplastics due to their excellent melt flow and re-solidification behavior.
⚠️ Considerations:
- Slower cycle times than ultrasonic methods
- Less compatible with high-speed, fully automated systems
- Insert alignment and temperature control are critical for consistency
🔊 Ultrasonic Insertion in Industrial Settings
How it works:
Ultrasonic insertion uses high-frequency vibration (typically 20 kHz) to generate frictional heat at the interface of the insert and plastic. This high-speed vibration causes the plastic to melt rapidly and flow around the insert’s barbs and knurls, which is simultaneously pressed into place.
Ultimately, the threaded insert is seated into the substrate in the same manner and would have the same pull-out resistance. However, the methodology of creating the heat to melt the substrate is different. IE Heat staking machines apply heat energy to the insert. Meanwhile, ultrasonic machines apply vibrations in the insert which, in turn, create frictional heat in the substrate.
🧰 Ultrasonic Required Equipment:
- Ultrasonic Welder with insert tooling to generate ultrasonic energy
- Ultrasonic Stock with Converter, Booster & Horn to convert electric signal to mechanical vibration
- Custom Tooling & Fixtures to securely hold plastic parts and inserts
- Power Supply to control power, amplitude, frequency and time
- Pneumatic or Servo-Driven Force Control to ensure inserts are precisely embedded
- QC Testing Tools including visual inspection and/or automated camera systems
- Cooling System to rapidly solidify plastic and boost throughput
- Vibration Zone Safety Enclosures to protect staff
✅ Advantages:
- High-speed insertion, ideal for automated lines
- Excellent repeatability in insert positioning and depth
- Minimal thermal exposure to the entire part
- Suitable for integration with robotics and vision systems
Ultrasonic insertion is particularly effective for thermoplastics with moderate stiffness and low filler content, especially when integrated into automated work cells.
⚠️ Considerations:
- Higher capital equipment cost
- May introduce localized stress in glass-filled or brittle plastics
- Process parameters (amplitude, pressure, time) must be precisely tuned
🏭 Heat-Set vs. Ultrasonic: Industrial Comparison
Feature | Heat-Set Insertion | Ultrasonic Insertion |
Cycle Time | Slower | Very fast |
Tooling Cost | Low to Moderate | High |
Automation Integration | Moderate | High |
Material Stress | Low | Moderate (can induce cracks) |
Material Compatibility | Broad | Somewhat limited |
Process Control Sensitivity | High (temp, time) | Very High (freq, pressure) |
🧠 Decision Factors for Engineers
When selecting an insertion method for industrial use, consider the following:
- Production Volume
→ Heat-set is suitable for lower volume or high mix.
→ Ultrasonic excels in high-throughput automation. - Part Geometry and Tolerance
→ Ultrasonic offers superior consistency in insert placement. - Plastic Material
→ Heat-set is generally safer for glass-filled or brittle materials. - Budget and Long-Term ROI
→ Heat-set has lower entry costs but Ultrasonic may reduce labor and improve takt time in high-volume runs.
✅ Conclusion
Both heat-set and ultrasonic insertion offer reliable performance for embedding threaded inserts in molded plastic components. The right choice depends on your production environment, material selection, and long-term automation goals.
When in doubt, prototyping both methods with your specific resin and part geometry—and validating joint strength through mechanical testing—can help guide your decision.
Where does CFI fit in?
At CFI, we offer a wide range of high-performance fasteners and threaded inserts designed for composites and plastics. Contact our team at 847-918-0333 or sales@componentsforindustry.com to learn how we can support your next engineering project.