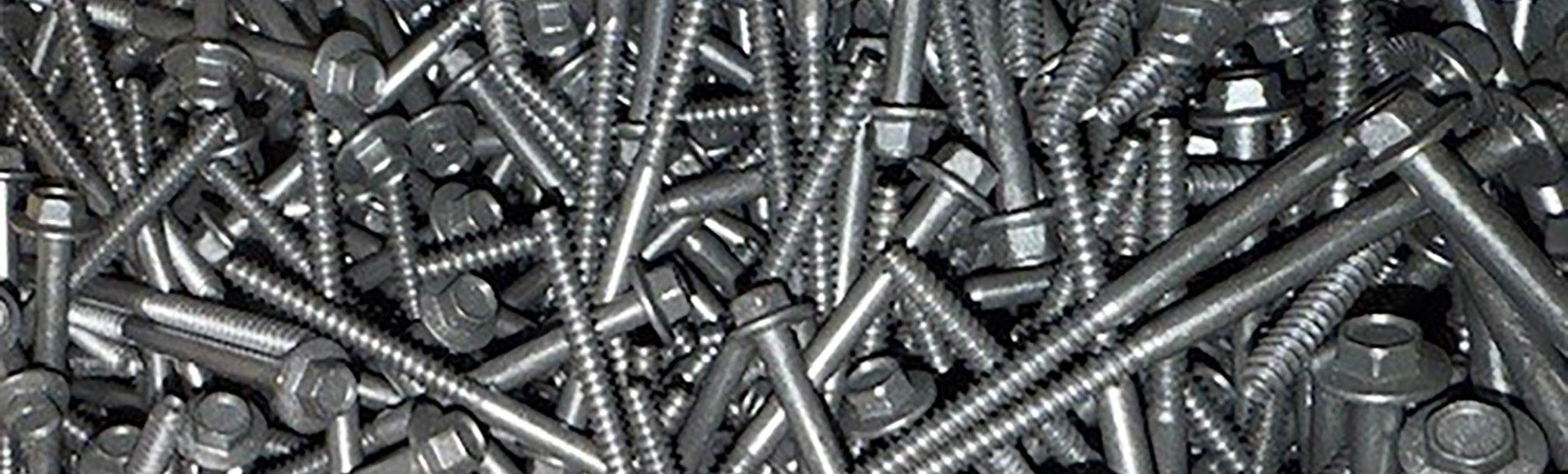
Balancing Strength, Speed, and Material Compatibility in Plastics and Carbon Fiber
As plastics and composites replace the use of metals in major industries, the question of how best to fasten complex assemblies is more relevant than ever. Self-tapping screws—fasteners that cut their own threads during installation—offer compelling benefits in these applications, but also come with limitations that engineers must consider.
Should engineers design their assemblies with these fasteners in mind? Should they avoid them and use threaded inserts and/or bosses instead? We will delve into these questions and more.
What are the Benefits of Using Self-Tapping Screws in Composites?
1. Simplified Assembly and Cost Reduction
Self-tapping screws’ key advantage is their ability to reduce component cost and simplify assembly. While some projects may require reinforcement through inserts or bosses, but, if joint strength is deemed adequate by product engineers, significant cost advantages can be gained through lack of parts and assembly cycle time.
In some substrates, adequate strength can indeed be gained from self-tapping screws alone. According to Mechanical Fastening of Plastics, “thread cutting screws provide adequate performance (however) ultrasonic insertion is not recommended in thermosets,” 1 (Lincoln, Gomes, Braden 92).
2. Strong, Reliable Joints in Thermoplastics
When properly designed from the ground-up by engineers with self-tapping screws in mind, these fasteners can form strong, vibration-resistant joints in both thermoplastics and composites. Thread engagement in ductile materials like ABS, polycarbonate, or nylon allows for robust load distribution and resistance to backing out under dynamic stress.
3. No Need for Secondary Fastening Hardware
Self-tapping screws reduce reliance on threaded inserts or weld nuts, which are often needed in composite assemblies. This makes these fasteners especially useful in applications that require weight restrictions. It also presents fewer opportunities for mechanical failure in high-performance environments such as automotive and UAV structures.
What are the Limitations of Using Self-Tapping Screws with Plastics & Composites?
1. Material Sensitivity – Carbon Fiber vs. Plastic
While thermoplastics including ABS, PE, PP and others can often withstand the radial forces of thread forming from self-tapping screws, carbon fiber composites have a harder time. These composites are often brittle and prone to delamination or cracking under similar stresses because the force is concentrated into a small area.
“Plastic deformations are likely to occur around the thread root, even if threaded fasteners are clamped with relatively low bolt force. Such plastic deformations are usually limited to small regions, since stress concentration factor is very high (however) the occurrence of plastic deformation does not necessarily lead to joint failure,”2 (Fukuoka 157).
Mechanical Fastening of Plastics summed it up best, “There are three major problem areas in the application of self-threading screws to plastics: (1) stripping during assembly, (2) cracking of the plastic material, (3) loosening of the joint because of material relaxation,”1 (Lincoln, Gomes, Braden 112).
For carbon fiber, thread-cutting screws (vs. thread-forming) with fine or specially designed flutes may reduce the risk of damage—but still require pilot holes and careful torque control.
2. Creep and Relaxation in Thermoplastics
Thermoplastics are prone to deforming under long-term loads – especially at elevated temperatures or during repeated heating and cooling like the starting and stopping of an ICE car engine. During this time, joints that rely entirely on self-tapping screws may experience loss of clamp, leading to loosening.
3. Installation Torque Control is Critical
The torque window for installing self-tapping screws into plastic or carbon fiber is narrower than in metals, requiring precise assembly controls. Excessive torque in plastics and CF may cause cracking, stripping, or material degradation, while insufficient torque can lead to poor thread formation and joint failure.
Design Best Practices for Self-Tapping in Composites
- Use thread profiles with shallow thread angles and radiused roots to reduce stress concentration in plastic.
- For carbon fiber, consider pre-drilled pilot holes and screws with cutting features and chip evacuation.
- Always verify long-term torque retention through thermal cycling and vibration testing.
- Where possible, include bosses or reinforced inserts in load-critical areas.
- Perform torque-to-failure testing during prototyping to define safe installation windows.
- Spreading out compressive load on the tightening of the fastener with a larger underhead bearing surface like a flat washer
Conclusion
Self-tapping screws offer real advantages for composite applications—particularly in plastics where speed and cost-efficiency are critical. But like all fasteners, their performance is dictated by thoughtful engineering. Understanding the mechanical behavior of the base material, screw geometry, and loading conditions is key to creating joints that last.
For load-critical or high-performance applications, a hybrid approach using threaded inserts or compression limiters may offer the best of both worlds: easy assembly and long-term reliability.
Where does CFI fit in?
For over 30 years, Components for Industry has been a worldwide provider in industrial components and a partner for industrial plastics and composites companies in a number of industries such as Automotive, Aerospace, Appliance and Heavy Industrial. If you want more information about CFI, our industrial components including self-tapping screws, contact us at 847-918-0333 or sales@componentsforindustry.com.