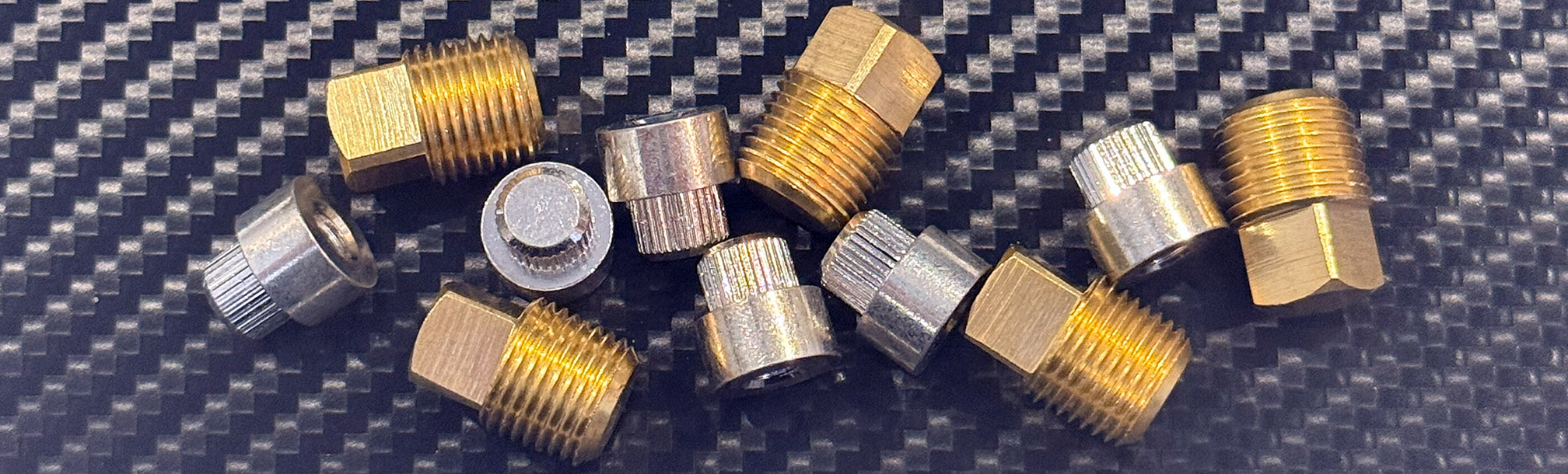
How to Select Fasteners that Match the Properties of Composites and Plastics
Arguably, nothing has revolutionized technological advancement and product design in key industries over the last 75 years like plastics and composites. Advancements in plastic and composite assemblies have driven advancements in key arenas such as aerospace, automotive, medical, consumer electronics, and renewable energy, just to name a few.
That said, complex assemblies in the 2020s and beyond often require support from custom-engineered fasteners. Choosing the correct fastener is a crucial decision for maintaining the performance, structural integrity and longevity of these assemblies. These decisions can also have greater downstream effects on the machine as a whole.
Understanding Composite and Plastic Material Properties
Composite materials, such as fiberglass and carbon fiber, achieve superior strength-to-weight ratios, corrosion resistance and durability. Both materials can be molded into complex shapes and lightweight designs. However, they can fall victim to delamination and cracking if screws or other fastening methods are deployed without the use of threaded inserts.
Engineered plastics such as polycarbonate (PC), acrylonitrile butadiene styrene (ABS), and polyethylene (PE) offer excellent durability and design flexibility for material and product engineers. However, they offer less tensile strength than either their carbon fiber or fiberglass counterparts. This makes traditional fastening methods without threaded inserts even less effective.
Challenges in Fastening Composites and Plastics
- Delamination and Cracking: Composite layers and plastic surfaces can crack or deform under localized stress such as point load stress, shear stress, impact stress, creep stress, tensile stress, and impact stress.
- Stress Concentration: Traditional fasteners can create high-stress points because the force isn’t evenly distributed across a composite material, this compromises structural integrity and leads to delamination in composites and deformation in plastics.
- Thermal Expansion: Differences in thermal expansion between fasteners and materials like carbon fiber, fiberglass, PC, ABS, PE and other plastics can cause loosening over time.
- Creep: Plastics are especially prone to deformation under continuous load, leading to joint loosening. While composites are less prone to creep, the danger still exists without the use of companion threaded inserts.
Key Considerations for Selecting Fasteners
- Material Environment Compatibility:
- Depending on deployment environment, using corrosion-resistant materials such as stainless steel, titanium, or reinforced polymers can help prevent material degradation in harsher environments.
- Load Distribution:
- Opt for fasteners that can distribute mechanical load evenly, such as the use of threaded inserts, to minimize stress on the material and prevent potential cracking and delamination in plastics and composites.
- Thermal and Environmental Resistance:
- Choose fasteners designed to withstand temperature changes and harsh conditions such as corrosive environments, mechanical vibration and UV radiation.
- Reduce Wear and Tear by Minimizing Drilling:
- Reduce wear and tear on plastic and composite structures by reducing the need for drilling. This can be achieved through the use of threaded inserts, transferring the mechanical load from the composite or plastic structure to the insert.
Types of Fasteners for Composite Materials and Plastics
- Threaded Inserts
- Threaded inserts, such as knurled, helical and press-fit inserts, are ideal for both composites and plastics. They spread the load over a larger surface area, reducing the risk of delamination and stress cracking.
- Blind Rivets
- Blind rivets, also known as pop rivets, and rivet nuts enable secure fastening without access to both sides of the material, ideal for automotive and aerospace applications. Blind rivets are typically found in body panels and interior components.
- Adhesive-Bonded Fasteners
- Bonded fasteners can provide threads virtually anywhere through the use of adhesives; eliminating the need for drilling altogether. This preserves the structural integrity of composites and plastics and is particularly effective for joining plastic components.
- Composite- and Plastic-Specific Screws
- Special screws with wide, shallow thread geometries specially tailored to grip softer materials like plastics and composites. Interlocking snap-fit designs that connect without either fasteners or adhesives are also commonly used in plastic assemblies.
Conclusion
Selecting the right fastener for composite materials and plastics is critical for ensuring durability, safety, and performance in advanced engineering applications. By considering material compatibility, load distribution, and environmental conditions, engineers can enhance the longevity and reliability of these assemblies.
Where does CFI fit in?
At CFI, we offer a wide range of high-performance fasteners designed for composites and plastics. Contact our team at 847-918-0333 or sales@componentsforindustry.com to learn how we can support your next engineering project.