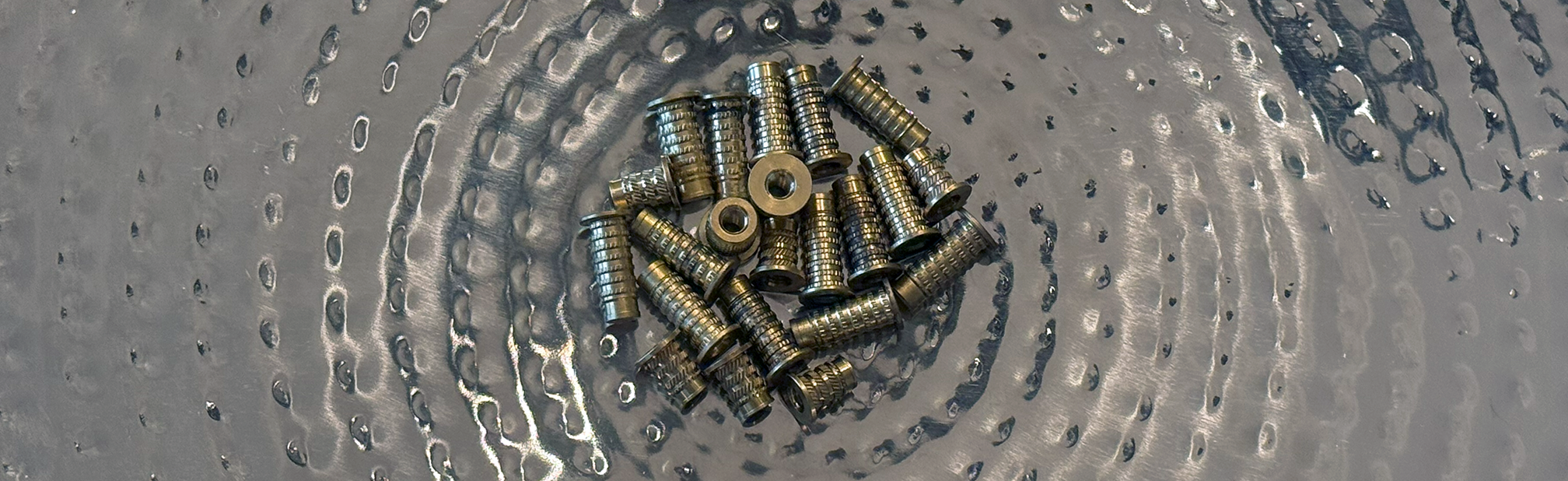
Exploring the Rising Need for Threaded Inserts Amid the Increasing Adoption of Aluminum in Modern Manufacturing
In 2019, according to the International Aluminum Institute, the automotive industry made up 18% of the world’s total aluminum consumption annually. That number is expected to more than double to as much as 335 million tons per year by 20501. This growth is illustrated by a 2022 study conducted by Ducker Carlisle for European Aluminum. This study concluded that an average car in 2022 could contain about 200 kg of aluminum, with projections estimating that number will grow to 251.5 kg by 20302. This growth is projected to be driven largely by the large-scale adoption of fuel efficient and electric vehicles.
Now, that kind of projected growth certainly leaves aluminum industry analysts bullish on the future of their industry. But where does that leave fasteners?
Where does the projected growth in aluminum leave the fastener industry?
Here at CFI, we project that not only would the use of this additional aluminum and other next-generation materials leave our industry in good hands, but ultimately, it boosts the need of one type of component in particular: the threaded insert.
The stated purpose of the threaded insert is to provide a durable, wear-resistant and reliable thread to softer, weaker or incompatible materials and are typically deployed to save weight. In the big three of most commonly used metals in manufacturing – Steel, Aluminum and Copper – Aluminum is widely seen as the weakest in terms of tensile strength.
With the projected growth of aluminum in the automotive industry coming in the next decade, it doesn’t take the biggest jump in logic to think that these automotive OEMs are going to need a lot of threaded inserts to go with their millions of tons of aluminum.
Why are threaded inserts good for aluminum?
Aluminum is widely regarded as the weakest of the three commonly used metals due to its low tensile strength, softness, and lower elastic modulus compared to steel and copper. That said, its lightweight nature make it ideal for alloys with other elements such as magnesium, silicon and copper, leading to widespread use in the automotive and aerospace industries.
Threaded inserts are ideal for pairing weaker and lighter materials such as aluminum with heavier metals such as steel. Threads cut directly into aluminum can be more prone to wearing out quickly. That’s where stainless steel or brass inserts can be used to prove stronger and more reliable threading solutions inside of the aluminum.
In addition, aluminum has a high thermal expansion rate when exposed to temperature changes. Threaded inserts made from metals with a more stable thermal expansion rate, can help maintain the integrity of the threads and prevent loosening.
What are the emerging growth opportunities for aluminum outside of automotive?
Beyond the aforementioned growth in the automotive industry, aerospace is also expected to increase its consumption of aluminum. Like automotive, aerospace is heavily dependent on vehicle weight to drive fuel efficiency. In 2022, the aluminum alloys aerospace materials market size was $4.63 billion – that number is expected to growth to $6.59 billion or 68.7 million tons by 20323.
The aerospace sector has seen a boost in demand for aluminum alloys due to their lightweight properties. Aluminum alloys, and more specifically, aluminum-copper-magnesium alloys have seen the largest uptick due to their strength-to-weight ratio in aerospace, aviation, military and defense industries.
Just like with the automotive industry, this increased demand in the aerospace industry represents what could be a bonanza in the threaded insert market. While aluminum alloys are undeniably stronger than base aluminum, 2000 and 7000 aluminum-copper-magnesium hard alloys are still good because thermal expansion alone would offset the strength gains of the harder alloys.
In addition, 2000 and 7000 aluminum alloys can also be brittle and can be prone to fracture4. Use of threaded inserts can offset these issues while retaining the strength of both the aluminum alloy and paired material the fastener is joining.
Conclusion
A new world is on the horizon for aluminum prospectors. This new world also represents opportunities for threaded inserts. Various types, such as helical, tapered, and blind inserts, offer enhanced strength and reliable threading in aluminum applications. One thing is certain, as the demand for aluminum rises, so too will the demand for the insert.
- CM Group. An Assessment of Global Megatrends and Regional and Market Sector Growth Outlook for Aluminium Demand. February 2020. Obtained from: https://international-aluminium.org/wp-content/uploads/2021/03/cm_2050_outlook_for_al_demand_20200528_4wycD18.pdf ↩︎
- Ducker Research & Consulting. Aluminum Content in Passenger Vehicles (Europe) – Assessment 2022 and Outlook 2026, 2030. Obtained from: https://www.duckercarlisle.com/european-aluminum-commissions-ducker-carlisle-for-aluminum-content-in-cars-study/ ↩︎
- Emergen Research. Aluminum Alloys Aerospace Materials Market to Reach USD 6.59 Billion By 2032 | Emergen Research. 12 December 2023. Obtained from: https://finance.yahoo.com/news/aluminum-alloys-aerospace-materials-market-122000527.html ↩︎
- Xing, M., Yong-gang, W., Zhao,xiu, J. Dynamic Fracture Behaviors of Selected Aluminum Alloys Under Three-point Bending. Science Direct. December 2013. Obtained from: https://www.sciencedirect.com/science/article/pii/S2214914713000391 ↩︎