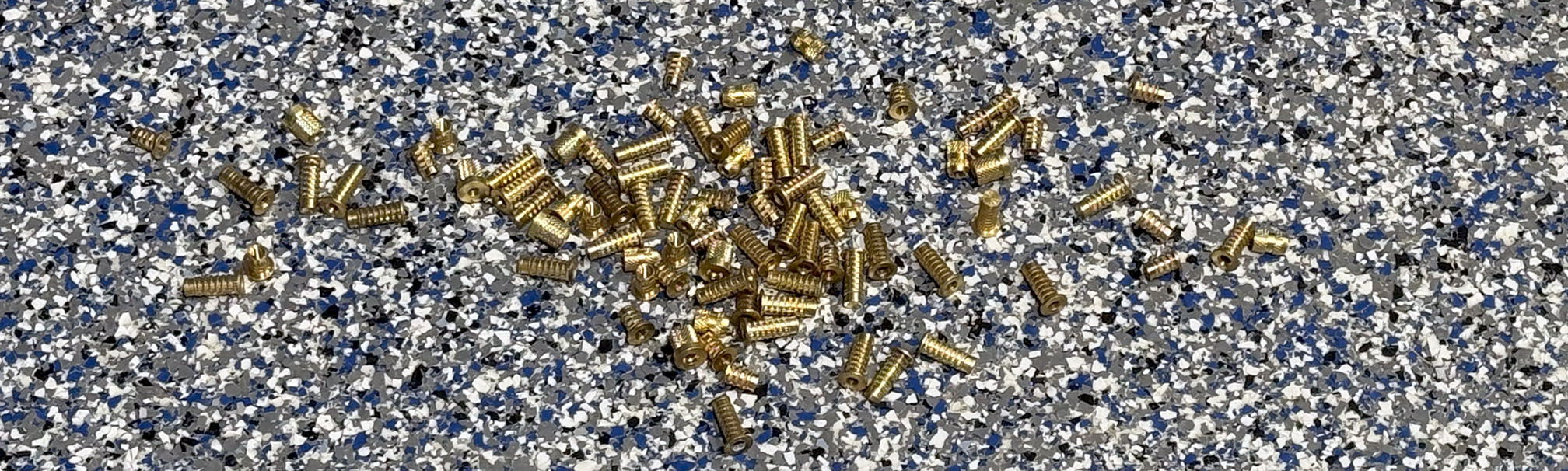
Every ounce counts in the aerospace industry. Meanwhile, strength is also at a premium because commercial aircraft like the Boeing 737 have to consistently fly upwards of 500 miles1 an hour while military aircraft like the F-35A Lightning II typically fly faster than two times the speed of most commercial aircraft2. These combined forces place aerospace engineers under pressure to save weight while boosting strength in both civilian and military aircraft.
Humble fasteners like the threaded insert have emerged as an essential solution, enabling lighter materials like composites and aluminum to be uses without compromising the structural integrity of the aircraft. From commercial planes that need to save fuel and help airlines hit profit margins to purpose-built military jets that need to save every ounce to outrun their adversaries, threaded inserts are key to improving performance, reducing weight, and ensuring long-term durability.
Why are threaded inserts used in aircraft?
Threaded inserts are used to create strong, wear-resistant threads in softer or more brittle materials, allowing lightweight alloys and composites to be fastened securely. For example, the Boeing 787 Dreamliner is well-known for its extensive use of carbon fiber-reinforced plastic – a polymer that shaved some 20% compared to traditional aluminum designs3. This material, while strong and extremely light compared to traditional metals like aluminum, is prone to thread wear such as fraying when rivets and bolts are mated directly into it. In addition, with a high-quality hole, a bolted joining enjoys many advantages over adhesive bonding including:
- Ease of assembly and disassembly
- Ease of part replacement
- Ease of repair
- Ease of inspection
- Ease of Airworthiness certification
- Tolerance to environmental effects4
Threaded inserts provide durable threads in these composite structures, ensuring fasteners stay secure without the risk of thread stripping, which could compromise safety. In addition, they allow for easy disassembly for inspection, something that is all but impossible with adhesives.
Applications in Aircraft
Threaded inserts are extremely versatile in aircraft, finding their way into various parts of the airframe. They are deployed as attachment points for avionics panels and access hatches to ensure easy maintenance without damaging the surrounding material. In addition, they are also used in engine components such as engine mounts to prevent thread wear and failure under extreme vibrations and heat. Finally, threaded inserts are used to secure lightweight interior components, from seats to cabin panels.
Where does CFI fit in?
For over 30 years, CFI has been a worldwide provider in industrial components such as brass inserts for a wide number of industries like Automotive, Aerospace, Appliance and Heavy Industrial. If you want more information about CFI, our industrial components or our custom design process, contact us at 847-918-0333 or sales@componentsforindustry.com.
- Adriana. How Fast Do 737s Fly? Explore the Cruise Speed of Boeing 737. Fly New Leaf. Obtained from: https://flynewleaf.ca/blog/how-fast-do-737s-fly/ ↩︎
- Air Force. F-35A Lightning II. Obtained from: https://www.af.mil/About-Us/Fact-Sheets/Display/Article/478441/f-35a-lightning-ii/ ↩︎
- Broberg, B. With Boeing 787, UW has a hand in revolutionizing aviation. University of Washington Magazine. Obtained from: https://magazine.washington.edu/feature/with-boeing-787-uw-has-a-hand-in-revolutionizing-aviation/ ↩︎
- Galińska, A. Mechanical Joining of Fibre Reinforced Polymer Composites to Metals – A Review. Part I: Bolted Joining. MDPI. Obtained from: https://www.mdpi.com/2073-4360/12/10/2252 ↩︎