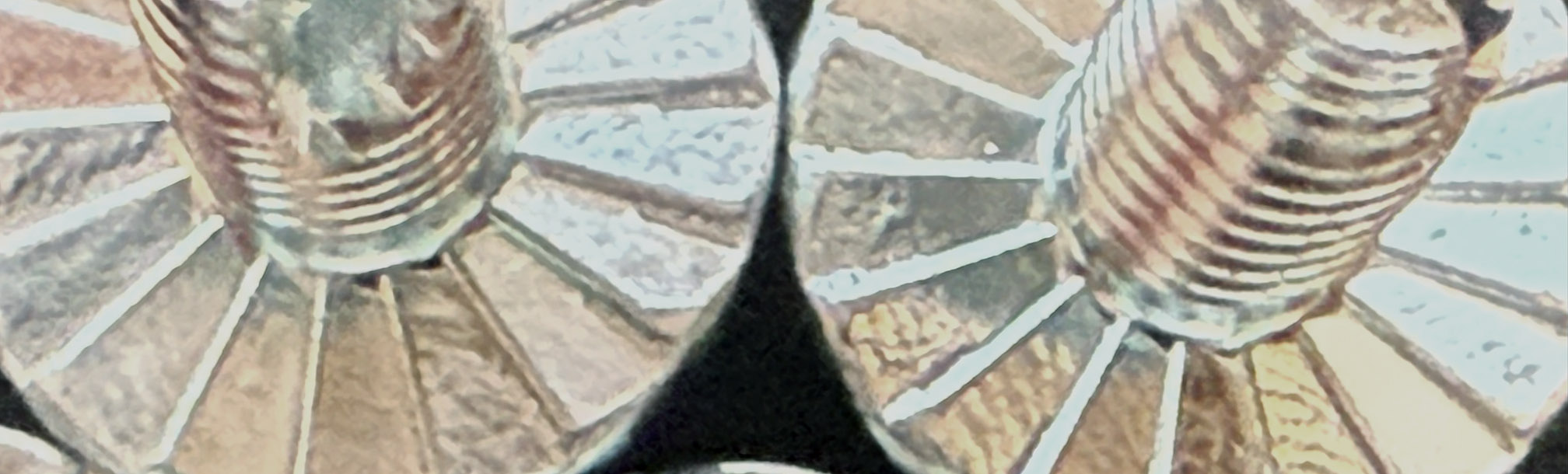
Explore the critical differences between plating, coating, and anodizing, and learn how each surface treatment impacts fastener performance, corrosion resistance, and application-specific design.
When designing assemblies for demanding environments, surface treatment is one of the most important fastener design decisions engineers can make. It is just as critical as fastener material or geometry. When designing a component, engineers must consider how environmental factors, such as corrosion, friction, and galvanic potential, can impact performance over time. Selecting the appropriate surface treatment can enhance corrosion resistance, optimize torque-tension behavior, and ensure compatibility with mating materials.
In this blog, we’ll examine three commonly used fastener surface treatments: plating, coating, and anodizing. We’ll also place an emphasis on their functional differences, performance trade-offs, and application-specific considerations.
Plating: Electrochemical Deposition for Functional Surface Properties
Sacrificial Coating Electroplating involves the electrochemical or autocatalytic deposition of a metal layer onto the surface of a fastener1. The fastener, or the substrate, is what the sacrificial layer is meant to protect. Generally the sacrificial layer is made from one of four materials – zinc, nickel, chrome and tin. The outer sacrificial layer is deliberately more prone to corrosion than the substrate in order to protect the fastener. This process is commonly used to enhance corrosion resistance, wear resistance, improve appearance, or introduce functional characteristics like conductivity.
Common Plating Materials
- Zinc (with or without chromate passivation)
- Nickel
- Chrome
- Tin
Plating Engineering Applications
- Zinc-electroplated carbon steel fasteners are typically used in automotive and heavy industrial applications for corrosion protection. In this case, the zinc sacrificial layer corrodes preferentially, leaving the steel substrate untouched.
- Nickel plating is often used in battery terminals and power connectors in EVs and consumer electronics. In this case, nickel plating is applied where increased hardness or conductivity is required because nickel’s resistance to tarnishing ensures long-term reliability.
- Tin plating is often used in electronics due to its excellent solderability, its cost-effectiveness and electrical conductivity.
Design Considerations
- Typical electroplating layer thickness ranges from 5 to 25 microns.
- Post-plate baking may be required for high-strength steel fasteners to mitigate hydrogen embrittlement.
Coating: Barrier Layers for Environmental Resistance and Assembly Control
Barrier Coating for components refers to the application of organic or inorganic compounds to form a protective barrier on the fastener surface. These coatings act like a physical barrier to create a seal around the substrate so corrosive agents never interact with the fastener. Unlike plating, coatings can be polymer-based, ceramic, or hybrid formulations.
Common Coating Types
- Organic barrier coatings (e.g., epoxy, acrylic, or polyester resins)
- Zinc-rich base coats with inorganic binders
- Fluoropolymer-modified films for low friction or chemical resistance
Coating Engineering Applications
- Zinc-rich coatings provides a physical barrier, isolating the substrate from corrosive elements. A sacrificial corrosion layer is key for structural and high-strength fasteners2.
- Polymer topcoats with controlled coefficient of friction are used where consistent preload is critical.
- Chemical-resistant coatings are specified in applications involving solvents, salts, or acids (marine, process industries).
- Common industries using fasteners with barrier coatings include the marine, automotive industry and heavy equipment due to resistance to liquids, salt spray, and hydraulic fluids; aerospace due to compatibility with composites as well as the above considerations.
Design Considerations
- Film thickness typically ranges from 10 to 100 microns.
- May impact thread fit and require tolerance adjustments in high-precision assemblies.
- Many coatings offer torque-tension control benefits but must be validated with in-application testing.
Anodizing: Electrochemical Conversion for Alloy Fasteners
Anodizing is a conversion process, typically in aluminum or titanium, where fasteners are oxidized in an electrolyte bath to form a controlled, thickened oxide layer. This thickened oxide layer, in turn, protects the substrate from direct contact from corrosive substances. Unlike plating or coating, anodizing does not add foreign material to the fastener.
Common Types
- Type I (chromic acid anodizing): thin, flexible and corrosion-resistant
- Type II (sulfuric acid anodizing): general-purpose, dye-accepting
- Type III (hardcoat anodizing): thicker, denser oxide for abrasion resistance
Engineering Applications
- Aerospace and electronics where lightweight, corrosion-resistant fasteners are needed.
- Hard-anodized fasteners used in high-cycle or abrasive environments.
- Anodized Fasteners are found in Aerospace, Automotive, EV and satellite applications for their corrosion and wear resistance as well as improved durability when exposed to vibration, pressure and temperature cycling.
Design Considerations
- Suitable only for aluminum and titanium substrates.
- Provides moderate corrosion protection unless sealed post-anodizing.
- Oxide layer is non-conductive, which can impact grounding or EMI shielding unless masked or modified.
Performance Comparison Table
Property | Plating | Coating | Anodizing |
Substrate Compatibility | Steel, brass, stainless | Broad (steel, aluminum, alloys) | Aluminum or Titanium |
Typical Thickness | 5–25 µm | 10–100 µm | 10–75 µm |
Corrosion Resistance | Moderate (zinc), high (cadmium) | High, depending on system | Moderate to high, if sealed |
Risk of Hydrogen Embrittlement | Yes (for high-strength steels) | No | No |
Electrical Conductivity | High (nickel, tin) | Low to moderate | Very low (unless modified) |
Torque-Tension Control | Variable, may require lubrication | Tunable via low-friction topcoats | Requires separate lubrication |
- What is Electroplating? BYJU. Obtained from: https://byjus.com/chemistry/electroplating-process/ ↩︎
- Jayashree R, Jaswanthi D K, Sharmila S. Analysis of hydrogen embrittlement in zinc electroplating. International Journal of Science and Research Archive. 18, May 2023. Obtained from: https://ijsra.net/sites/default/files/IJSRA-2023-0369.pdf ↩︎
Selection Guidelines for Engineers
When evaluating surface treatments, engineers should weigh the following factors:
- Environmental exposure: salt, moisture, UV, chemicals
- Mechanical stress: abrasion, impact, preload consistency
- Electrical requirements: conductivity, insulation, EMI shielding
- Compatibility: galvanic potential between dissimilar metals
- Assembly method: torque-limited, tension-limited, interference fit
In fatigue-critical or corrosion-prone joints, surface treatment can directly influence service life, torque accuracy, and long-term reliability.
Conclusion
Plating, coating, and anodizing each serve specific engineering objectives. Plating offers conductivity and basic corrosion resistance; coatings provide robust barrier protection and torque control flexibility; anodizing is ideal for aluminum where durability and weight savings are priorities.
Choosing the correct finish of your design’s fasteners is not just about cost or appearance. Instead, it’s a performance decision that should align with the mechanical, environmental, and functional demands of your design.
Where does CFI fit in?
Need help determining the right surface treatment for your fastener application? CFI’s engineering team has been assisting companies with material compatibility, torque-tension studies, and design-for-manufacturability support for over 30 years. We’ve been a partner in a number of industries including Automotive, Aerospace, Appliance and Heavy Industrial. If you want more information about Components for Industry, contact us at 847-918-0333 or sales@componentsforindustry.com.