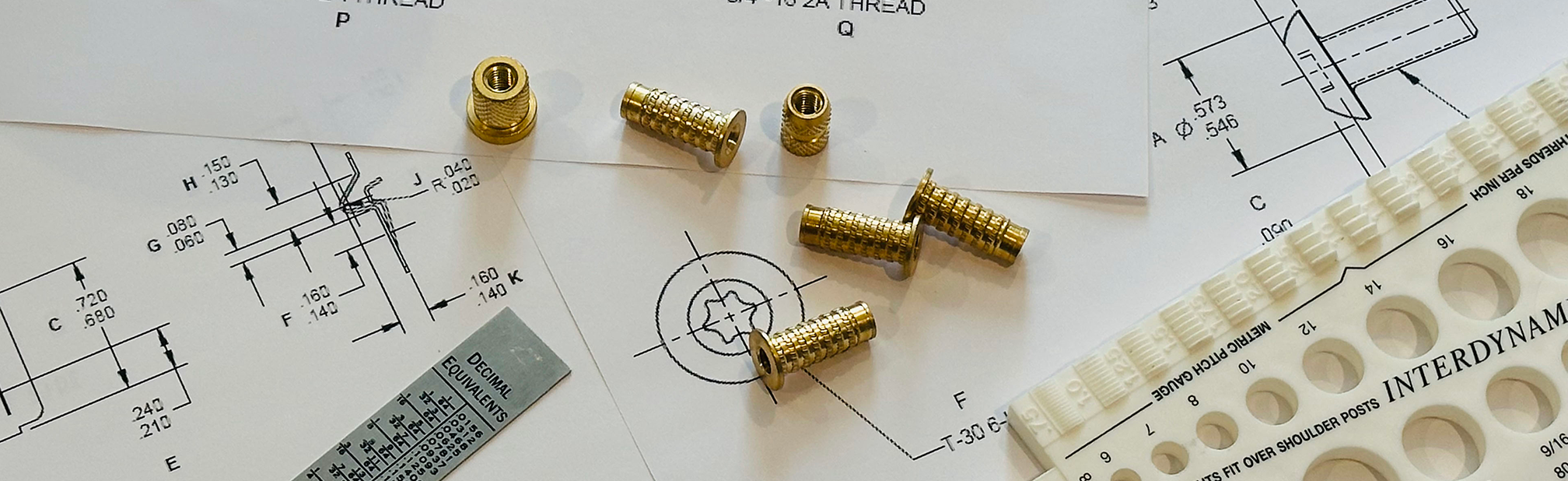
How CFI’s ISO certification ensures consistent quality management and how it applies to the component industry
Regardless of the industry, quality management is essential for success – especially with today’s discerning customers. In order to deliver a high-caliber product, that standard must go all the way down to the base elements that it is built from, including the fasteners that hold the machine together. As a leading Quality Management System, ISO:9001:2015 ensures that companies like Components for Industry are consistently striving for product quality; streamlining operations; and meeting customer expectations.
CFI has been an ISO:9001 certified components company for decades. Upholding International Organization for Standardization’s (ISO) standards of excellence has enabled CFI to place a stronger emphasis on risk-based thinking, leadership engagement, and helped us align quality management with the strategic direction of our company.
What is ISO 9001:2015?
ISO:9001:2015 is part of the larger ISO 9000 family of quality management standards built for organizations looking to improve their QMSs and developed by the ISO organization. The major revision in 2015 introduced key changes that promoted a risk-based approach to quality management, increased flexibility in documentation, and a focus on leadership and customer satisfaction.
At its core, ISO 9001:2015 is based on a focus on the customer. In order to deliver said focus, there must be buy-in and engagement at all levels of the organization including top management; viewing all activities as interconnected activities and working to improve consistency; continuous improvement on processes to improve quality; evidence-based decision making; and relationship management to foster good communication with all stakeholders including suppliers.
How does ISO:9001:2015 differ from past versions of ISO:9001?
ISO:9001:2015 differs from previous versions of ISO:9001 such as ISO:9001:2008 such as updates that reflect more modern business needs. ISO’s current 2015 format adopted a risk-based approach at a more systemic level before they arise. This requires organizations to identify, assess, and address risks and opportunities proactively throughout the Quality Management System. Before, in ISO:9001:2008, Clause 8.5.3, ISO was focused more on preventative action on issues in isolation.
For example, in the fastener industry, in ISO 9001:2008, a component manufacturer might focus on preventative action by ensuring raw materials are inspected to prevent defective fasteners from being produced. Meanwhile, under ISO 9001:2015, such a manufacturer would analyze the broader risks by looking at the supplier reliability, market fluctuations, shipping delays, in addition to raw materials and implement controls to reduce the impact on production timelines and quality. This shift to a broader focus makes ISO 9001:2015 more flexible and more realistic in today’s ever-changing business world.
Why is ISO:9001:2015 important in the fastener industry?
Components like nuts, bolts, screws, rivets, et al may seem small in the grand scheme of automobiles, airplanes, and appliances, but their quality is so critical to the performance of larger systems. Poorly manufactured components can lead to larger structural failures and even costly recalls at the manufacturer level. For manufacturers and suppliers of fasteners, ISO 9001 offers benefits including:
- Consistency in Product Quality: ISO 9001 requires manufacturers and suppliers to establish documented processes for production, inspection and testing. This consistency in processes ensures that every component produced meets the same requirements, drastically reducing the risk of defective product reaching customers.
- Customer Satisfaction: As we’ve covered before, ISO 9001 places a large emphasis on placing customer needs first. By focusing on customer requirements, component companies like CFI can build stronger relationships with clients, leading to repeat business.
- Reduced Waste & Increased Efficiency: This tenet has become more important as we move forward in the 2020s. ISO 9001 encourages a process-based approach, meaning that every process step is analyzed for operational efficiency. This can help reduce costs for the end customer by improving delivery times.
- Continuous Improvement: In addition to waste reduction, there is a constant push toward improvement of processes within CFI including regularly assessing processes and identifying areas for improvement. This allows us to take action to enhance product quality, efficiency, and customer satisfaction over time.
- Regulatory Compliance: CFI works within highly-regulated industries like automotive and aerospace. Being ISO 9001:2015 certified demonstrates to our clients that we can navigate these regulatory requirements.
- Evidence-Based Decision Making: Within the tenets of ISO 9001:2015, there is a strong emphasis on making decisions based upon data, measurements, performance metrics, and processes. In essence, decisions in the component industry must be made upon cold, hard facts, nothing more, nothing less.
For components companies like CFI, implementing ISO 9001:2015 was more than just a box to check. It was a strategic investment in our company’s future and included a top-down retraining of our workforce. In an increasingly-competitive industry where customers expect precision and reliability, being ISO 9001-certified is simply a necessity.
How can CFI help with your company’s Quality Control?
For over 30 years, Components for Industry has been a worldwide provider in industrial components and services like quality control for a wide number of industries like Automotive, Aerospace, Appliance and Heavy Industrial. If you want more information about CFI, our industrial components, our threaded inserts, or our custom design process, contact us at 847-918-0333 or sales@componentsforindustry.com.