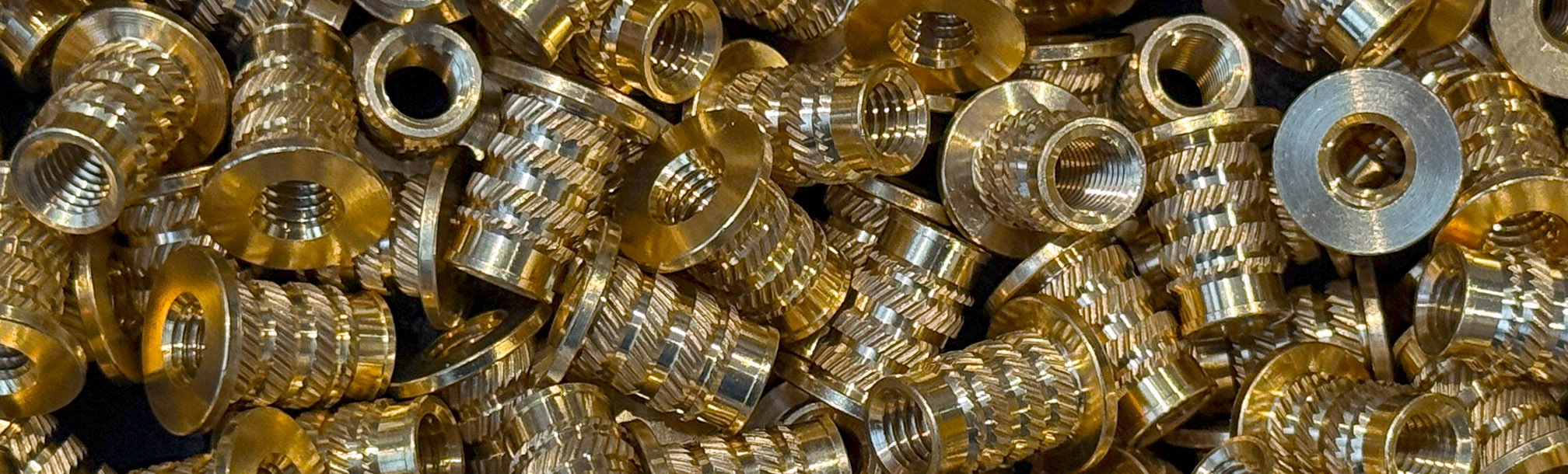
How to choose the best fasteners for plastic and composite materials in dynamic-load environments
You’ll find composite materials in everything from everyday kitchen gadgets to high-performance electronics in cars and airplanes. That’s why engineers in these industries must select fasteners can withstand the intense vibration and dynamic stress that come with them. When engineers use plastics, carbon fiber, and fiberglass, issues from vibrations can be compounded by material brittleness, viscoelasticity, and low thread retention.
Careful fastener selection is essential to avoid loosening, joint failure and material degradation in high-motion environments. This blog outlines some strategies and fastener types that can provide vibration resistance in plastic and composite assemblies.
Why are Composites Vulnerable to Vibration Loosening?
Compared to metals, composite materials lack elasticity and surface friction that are needed to maintain preload in bolted joints. Elasticity and surface friction are the key forces that keep fasteners tight.
In addition, composite materials are prone to substrate damage issues that can reduce clamp force significantly including:
- Creep and relaxation
- Delamination or cracking under high localized stress
- Low thread shear strength, making stripping more likely with repeated movement
These issues are only magnified under vibratory loads, especially in high-speed equipment such as vehicle assemblies, or industrial machines.
What are Some Fastener Features That Can Improve Vibration Resistance?
High-vibration environments are never ideal for either the substrate or the fastener. That said, there are some fastener features that your engineers can incorporate to ensure that both the fastener and the plastic and/or composite material can withstand the vibratory load.
1. Threaded Inserts
For composites like carbon fiber or thermoplastics, threaded inserts (especially those with knurled or helical designs) can remove the forces of the vibration from the substrate and place them on the insert themselves. This makes inserts an excellent thread retention tool via load distribution1 (Lincoln et al., p. 16).
Threaded inserts:
- Prevent stripping under dynamic load
- Isolate the screw from the plastics / composite, reducing damage
- Allow for consistent torque application and repeatable assembly/disassembly
2. Thread-Locking Features
Fasteners with integrated locking features—such as nylon patches, serrated flanges, or thread-forming interference designs—help maintain torque in dynamic assemblies.
- Nylon patch screws add frictional resistance without damaging the substrate.
- Serrated underheads or flanges improve grip on the mating surface, helping maintain clamp even as the composite material shifts.
3. Prevailing Torque Fasteners
These are specially designed screws or nuts that resist loosening through inherent friction in the threads, typically via a deformed thread section or elliptical geometry. These are ideal when no adhesives or patches are allowed due to heat or chemical exposure.
4. Use of Retainers or Washers
Adding spring washers, Belleville washers (conical spring washers), or wave washers helps maintain clamp force in joints where the composite may relax or compress over time. These components help accommodate small dimensional shifts and ensure preload stability.
Applications That Demand Vibration-Resistant Fasteners
- Automotive dashboards and instrument panels
- Aerospace composite fairings and access panels
- Electric motor housings and drive units
- Consumer electronics subjected to motion or handling
- Medical devices with mobile components
Conclusion
Vibration resistance in composite assemblies isn’t just about choosing the right fastener—it’s about creating a system that accounts for the mechanical limitations of the material. By combining engineered fastener designs, reinforced inserts, and clamp-stabilizing elements, designers can prevent joint failure and extend product life in demanding, high-motion applications.
As composite usage continues to grow across industries, fastening strategies must evolve to match—and vibration resistance should always be at the forefront.
Where does CFI fit in?
For over 30 years, Components for Industry has been a worldwide provider in industrial components and a partner for industrial plastics and composites companies in a number of industries such as Automotive, Aerospace, Appliance and Heavy Industrial. If you want more information about CFI and our industrial components custom-engineered for plastics and composites, contact us at 847-918-0333 or sales@componentsforindustry.com
Citations
- Lincoln, D., Gomes, C., & Braden, P. Mechanical Fastening of Plastics. McGraw-Hill, 1998. ↩︎