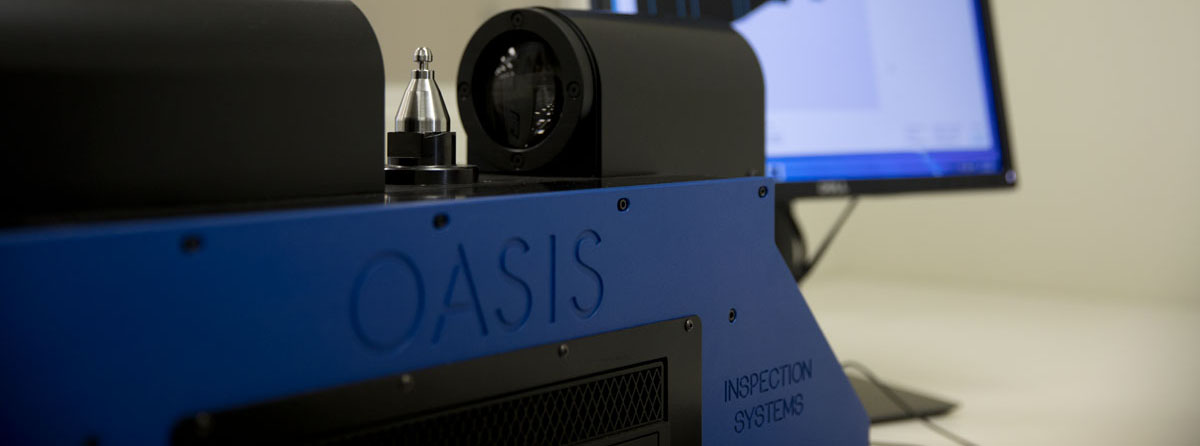
Quality Control in the component industry demands top-tier equipment—here’s what it is and how it helps clients
The QC department plays a vital role in the industrial component industry, however there is a big difference between a world class QA/QC operation and a more pedestrian operation. In a standard industrial component company’s QC department, there are some tools that you will always find including calipers, micrometers, gauge pins and thread gauges. However, CFI has invested in its operation to ensure our clients don’t just have the basics, but have the next level.
What are the basic industrial component QC tools and how are they used?
In an industrial component setting, basic tools such as calipers, micrometers, pins and thread gauges are used to measure the basic dimensions of nuts, bolts, screws and other components. Typically, calipers are utilized to measure the diameters of bolts, screws, and other cylindrical parts. Micrometers precision measuring devices that are used to measure dimensions for small parts such as screws, nuts and bolts. They are used to measure dimensions such as depths of holes and recesses; pitch diameter; and narrow grooves and slots.
Gauge Pins are cylindrical rods that measure hole diameters, roundness and straightness. Gauge pins themselves are used in a “Go/No-Go” method where if a hole tolerance is within a 4.00 ±0.01 mm, a 4.01 mm pin (No-Go) should not fit, ensuring that the hole is not too large. Thread Gauges are used to measure and verify the dimensions and quality of threads of screws, bolts, nuts and other threaded industrial components.
What other QC tools does Components for Industry use?
In addition to the standard toolset of the calipers, micrometers, pins and thread gauges, CFI employs high tech solutions such as our OASIS (Optical Automatic Smart Inspection System) machine, Micro-Vu, X-Ray, load tester, hardness tester, and surface roughness tester.
What is an OASIS Inspection System and what capabilities does it give our QC Department?
An OASIS inspection system marries the capabilities of a Comparator, CMM, height gauge, calipers and micrometer and is accurate to ±0.0001 inches. The system is also non-contact and less prone to human error as it is automatic focus and saves its own images. It provides our QC team with real-time feedback and enables quick corrective actions, reducing scrap rates and improving overall production quality. In addition the CFI QA/QC team has been utilizing OASIS equipment for over a decade, ensuring additional peace of mind with our clients’ components.
What is a Micro-Vu and what are its capabilities?
Micro-Vu is a high-precision measuring and inspection system that can measure dimensions, angles, radii, and other features of components from the automotive, aerospace and appliance industries down to the micron. It also provides a detailed report of all the parts in a batch and can even measure the 3D contours of components to ensure that it conforms to original design specifications. Like our OASIS Machine, the CFI QC team has been utilizing our Micro-Vu for several years, providing our clients confidence in the quality of our components.
How is an X-Ray machine used in a components setting?
X-Ray machines are familiar in a medical setting, but they also play a crucial role in an industrial components QC department by giving testers an inside look at a component’s plating composition and thickness. We typically check the chemical composition range of a component’s stainless steels to verify if the material is truly 302, 316 or 400, etc.
In addition to defects, we can also use X-Ray Fluorescence (XRF) to verify the composition of plating and ensure that the correct metals and alloys were used during the manufacturing process. For example, an XRF test can confirm that a stainless steel part has the correct amount of chromium and nickel to ensure that it well have the necessary corrosion resistance.
What are load testers, hardness testers, and roughness testers and what do they do?
Load Testers is a gauge and stand that measures the compression or extension force on a spring. Its job is to test the maximum pulling force (tensile strength) and how much compression (compressive force) a component can withstand before breaking. Load Testers can also be used for Shear Testing and Fatigue Testing to determine how many cycles a part can undergo before failure.
Hardness testers use different attachments to create an indent on the surface of a part. This is done to measure a component’s resistance to indentation, wear and scratching. Finally, the surface roughness tester uses a needle to scratch across a surface of a part and measure essentially the mountains and valleys on a part. A surface of 0 is perfectly smooth and when spec’d on a drawing, it will call for a specific RA (RA is the roughness designation).
How can CFI help with your company’s Quality Control?
For over 30 years, Components for Industry has been a worldwide provider in industrial components and services like quality control for a wide number of industries like Automotive, Aerospace, Appliance and Heavy Industrial. If you want more information about CFI, our industrial components, our threaded inserts, or our custom design process, contact us at 847-918-0333 or sales@componentsforindustry.com.