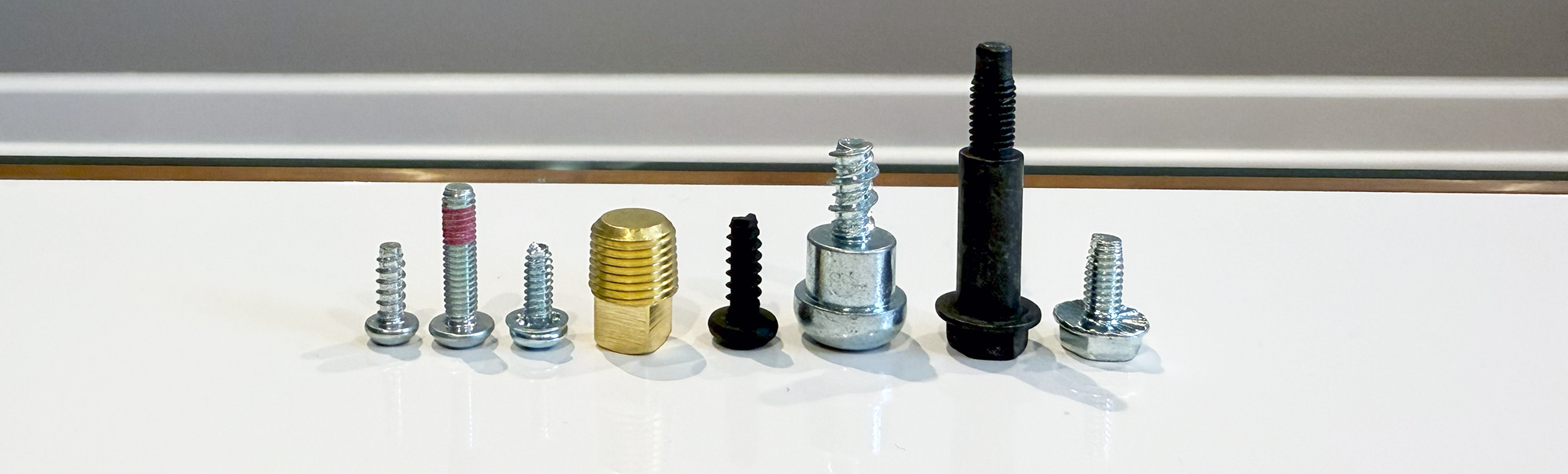
When you learn about the components industry, you can truly get into the weeds about the different types of threads. Here is a complete breakdown of the most commonly used thread types. While the most common types of threads are straight threads and tapered threads, there are several other types of threads that deserve mention.
To go in depth with straight threads (also called Parallel Threads), there are several subtypes of this types of thread including the Unified Thread Standard and their Metric Thread variants.
Unified Thread Standard (UTS)
Unified National Coarse (UNC)
UNC threads are known for their coarse thread and are used for general purposes where quick assembly is required. Screws with UNC threads feature general tolerances are built to allow for manufacturing errors and are more resistant to wear and damage. UNC threads, like all other UTS threads have a 60-degree flank angle.
Unified National Fine (UNF)
Unified National Fine threads are deployed where tighter, more precision fits are required. They are also known for a stronger hold in thin-walled materials such as maritime, automotive and medical applications.
Unified National Extra Fine (UNEF)
Unified National Extra Fine threads are used are utilized in applications in very tight fits in high-precision applications such as aeronautical or aerospace applications.
Metric Thread
Metric Coarse (M)
Most commonly used in Europe and Asia, Metric Coarse thread is essentially similar to UNC but designated by the letter “M” followed by the nominal metric diameter and pitch as opposed to the English diameter and pitch of the United National Coarse diameter and pitch. Metric Coarse threads feature a flank angle of 60 degrees.
Metric Fine (MF)
Similar to UNF, except using metric diameter and pitch and designated by the letter “M.” Again, similar to United National Fine, used for applications for more precise fits such as industrial applications like hydraulics and pneumatics. MF threads have a flank angle of 60 degrees.
As for Tapered Threads, there are metric tapered, BSPT, and NPT/NPTF thread. What unifies all tapered threads is that their diameter is not constant in these threads. It either increases or decreases as the thread length advances.
Other Thread Types
ACME Thread
ACME thread forms offer better engagement and strength compared to other standard thread due to a large surface area. ACME threads has a 29-degree flank angle while similar trapezoidal threads have 30-degree flank angles. As a result, they are most commonly used in high load capacity applications such as power transmissions, heavy machinery, railway systems and other high-capacity applications.
Trapezoidal Thread
Highly similar to ACME threads and adopted in Europe, trapezoidal threads have a thread form with a large surface area for a greater load distribution. Trapezoidal threads feature a flank angle of 30 degrees and an included angle of 60 degrees between the flanks. This provides a good mechanical efficiency due to angled flanks. Trapezoidal threads are typically utilized in linear motion systems like CNC machines, lathes and milling machines; power transmissions, vices and clamps; and large-scale heavy machinery. The advantages of Trapezoidal Threads are load capacity and reduced wear thanks to its distribution of high loads as well as efficiency of angled flanks to reduce friction.
Buttress Thread
Buttress Threads have an asymmetrical thread form and are used in applications where force is applied in one direction. Buttress threads have a 45-degree flank angle and a 7-degree angle on the weight bearing surface. Like ACME threads, Buttress Threads are used in heavy machinery and large equipment.
Square Thread
Square threads are just like they sound – made up of 90-degree angles forming squares with a flat top and bottom with vertical sides. With a square profile, it allows for uniform load distribution along the thread, reducing the radial stress. Square threads are typically used in high load applications like transmissions, presses, lifting equipment like screw jacks, and clamping devices because of its lack of power loss due to friction and high efficiency.
MJ Threads
Typically utilized in the aerospace, aeronautic, spacecraft and automotive industries where high stresses and high temperatures are required. While MJ and M threads have many similarities including a 60-degree flank angle, the difference between MJ and standard or M threads is the basic tooth height. The tooth height of MJ threads Is lower and features a rounder tooth than standard or M threads. This lower tooth height and rounder tooth reduces the stress concentration and fatigue life, making MJ threads ideal for high-stress applications.
National Pipe Thread (NPT)
As you would expect, National Pipe Thread is utilized primarily for joining pipes and fittings for plumbing and natural gas service line applications. Like other threads, NPT features a 60-degree thread angle. NPT threads are highly standardized and designed to create leak-proof seals between pipes and fittings where male and female threads are joined.
Where does CFI fit in?
For over 30 years, CFI has been a worldwide provider in industrial components such as screws and bolts for a wide number of industries like Automotive, Aerospace, Appliance and Heavy Industrial. If you want more information about CFI, our industrial components or our custom design process, contact us at 847-918-0333 or sales@componentsforindustry.com.