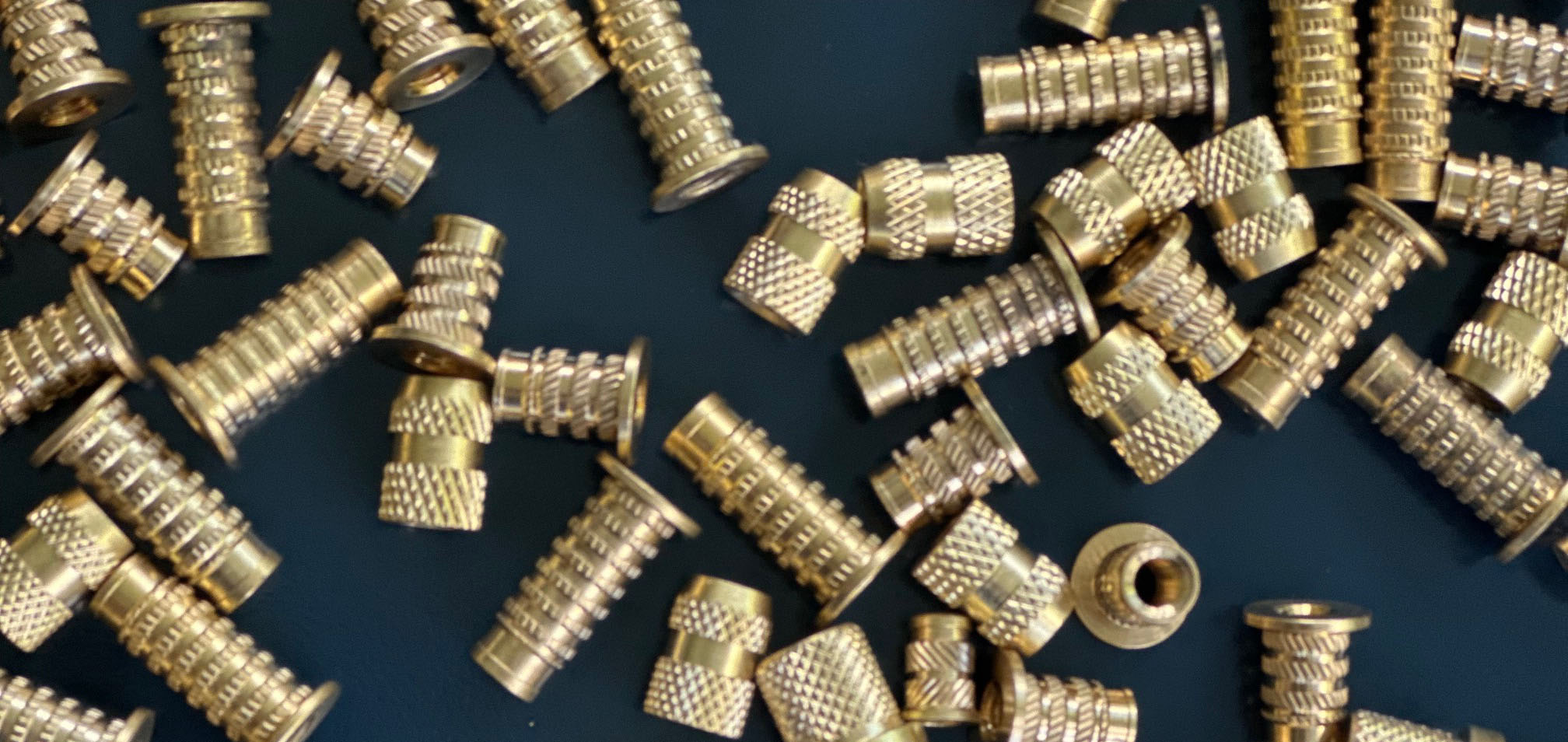
At CFI, we typically engineer custom screws, nuts and bolts for any application, however, our expertise doesn’t end there. Today we will be going over a component called brass inserts. We’ll answer basic questions like what they are, what they do, why they’re often made of brass. In addition, we’ll go over what recent advancements engineers have extracted from brass inserts in recent years.
What are brass inserts and where are they used?
In its most basic terms, an insert is used to turn a pre-drilled, unthreaded hole into one with threading. These inserts are typically used in tandem with softer materials such as aluminum, plastics, composites or even woods that would normally get damaged with the use of hard fasteners. Inserts can even be used to repair and reestablish the threading for a stripped hole. Essentially, if the base material is soft, a threaded insert might be added to introduce some strength into the design.
The insert gives the base material both added strength as well as reliable threading, providing a durable anchor point for screws, bolts or other fasteners. Threaded inserts are typically made from brass, steel and other types of materials are used in several industries and you’ll find inserts utilized in everything from Automotive to Aerospace and Defense to Electronic to Heavy Industrial to the furniture kits that you build in your living room. Basically, like any component, you’ll find them everywhere.
Why are threaded inserts often made from brass?
Brass presents a happy medium of several factors including strength, relatively cost, corrosion resistance, machinability, and brass is non-magnetic. These factors make brass an ideal material for inserts in many applications.
Can brass inserts be used in injection molding?
Brass inserts are commonly used in the injection molding process as a way to create strong, reusable metal threaded joints within plastic parts. These brass inserts can be used in both thermoplastics and thermosets and are not affected by plastic material stress relaxation.
Threaded inserts offer a stronger option than standard components alone. In fact, threaded inserts offer more pull-out torque on a mating part and keeps the threaded joint intact for the duration of the application than a self-tapping screw in plastics.
They also offer an excellent option for applications that require maintenance and need to be repeatedly taken apart and put back together unlike single-use self-tapping thread. The threaded insert’s strength enables the end user to take apart the plastic again and again. In addition, are not prone to self-tapping screw creep.
Why might they be made of brass over other materials such as steel?
If inserts aren’t made of brass, they are typically produced from materials like steel or stainless steel. Brass might be chosen thanks to its weight and corrosion advantage over steel. Engineers might utilize brass over steel or stainless depending on the application. Thanks to its weight savings, cost savings, and easy machinability, brass is typically used with softer materials like plastics, woods and composites.
You might utilize brass inserts when:
- There is a presence of hot, cold or salt water (such as a marine environment)
- Cryogenic applications where the operating temperature is extremely low
- Mild alkaline and lightly-acidic solutions (But not highly-acidic solutions)
- Petroleum-based materials
However, if there is no danger of corrosion, steel inserts might be utilized over brass inserts thanks to its relative cost savings. In addition, steel offers small thread strength advantage over brass inserts.
What are challenges engineers face when working with inserts and how are they addressed?
As versatile as brass inserts are, engineers face numerous challenges when they implement them into designs. First, engineers must ensure that materials must be compatible with both the insert and host materials. Mismatched materials can lead to numerous issues including corrosion, galvanic reactions and poor adhesion. All three issues can be overcome by considering chemical compatibility, thermal expansion coefficients and mechanical properties.
What advancements have brass insert engineers made?
In recent years, engineers have focused on developing new brass alloys to maximize tensile strength to improve wear and corrosion resistance. In addition, other advances such as new, non-magnetic and lead-free alloys have led to brass inserts being used in medical conditions. With these new alloys, engineers have also made advancements in surface treatments such as coatings and finishes. These treatments have led to reduced friction and improved wear and tear. This has led to longer average lifespan on brass inserts and reduced corrosion – working hand-in-hand with the new alloys.
What manufacturing process improvements have brass insert engineers made?
Along with the above improvements, there have been amazing improvements in the basic manufacturing processes for component manufacturers. This has led to impressive gains for the reliability, strength and lifespan for components like brass inserts.
These processes, in addition to processes like microfabrication have reduced the risk of thread stripping or galling in the assembly process in a wide range of industries.
Where does CFI fit in?
For over 30 years, Components for Industry has been a worldwide provider in industrial components such as brass inserts for a wide number of industries like Automotive, Aerospace, Appliance and Heavy Industrial. If you want more information about CFI, our industrial components, our brass inserts, or our custom design process, contact us at 847-918-0333 or sales@componentsforindustry.com.